WATCH FULL CUSTOMER STORY BELOW
In the fabrication industry, staying ahead of your competitors is always crucial. With continued technological advancements, businesses need a well-rounded arsenal of machinery that allows them to be the most efficient in their space. Customers want to see efficiency. If you can do a job more efficiently than your competitor, the customer will return to you every time. This is where an investment in CNC machinery can come in. Moving from manual to numerically controlled processes can significantly improve efficiency and productivity.
H&H Metals is a family-owned architectural sheet metal fabricator out of Thornton, Colorado. They were on the search for a new machine tool to keep them staying competitive in their space. They needed an efficient way to mill long bars. With the help of FlexCNC, they found a vertical machining center that helped solve the problems they were encountering. In 2020 they purchased a FlexCNC C-20-02 vertical mill.
H&H Metals is an architectural sheet metal fabricator that has been family owned since 1980. They are also a full-service steel and plate-based shop with a welding department. H&H Metals caters to the construction industry by providing components for glass and glazing contractors.
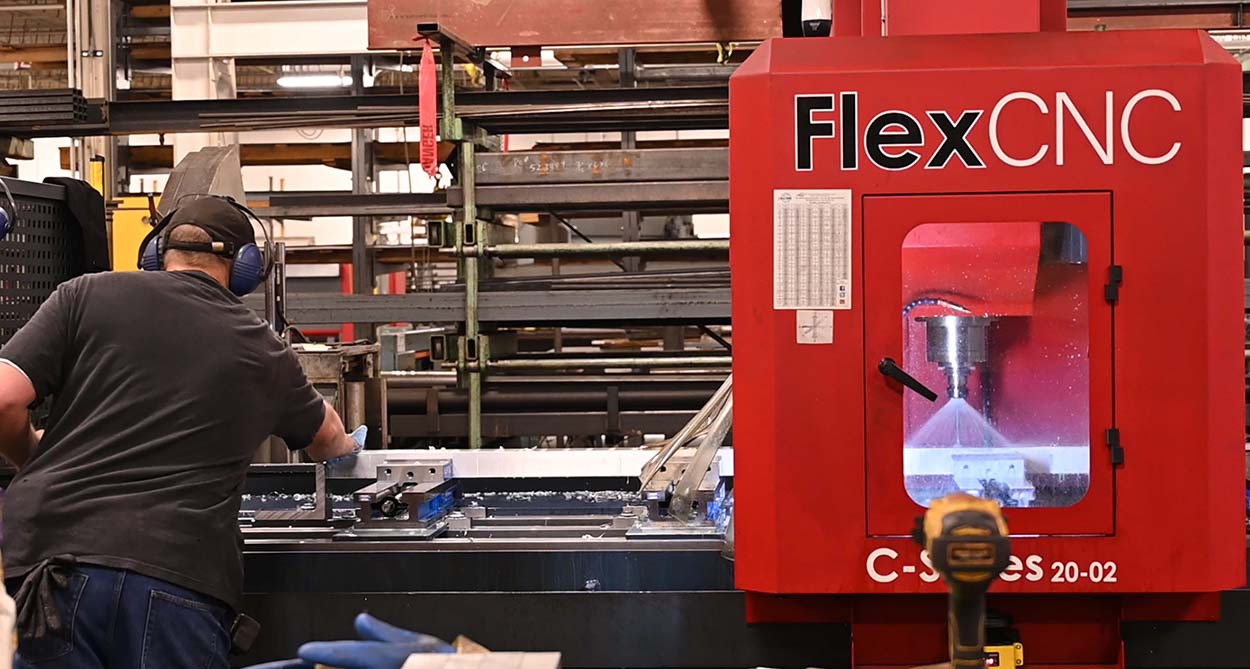
Life Before FlexCNC
Before investing in the FlexCNC, Chad Huff president of H & H Metals, said they produced all their parts manually. They purchased the FlexCNC because they needed to mill long bars and get them dead straight. Many glazing contractors were asking them to build steel inserts to go inside extrusions, and they found that their manual mills were too inefficient.
Using a manual mill, they machined a 20-foot bar three feet at a time, which required a substantial amount of repositioning. The manual process left room for human error and took a lot of time to get finished parts to customers. They also tried making the parts on the laser but introducing the material to heat caused the inserts to warp and wouldn’t fit into the extrusions. The FlexCNC made this machining process effortless, allowing them to increase machining efficiency and further satisfy their customers.
Machining Small Parts Efficiently
Once the FlexCNC was installed and running, H&H went to work and saw immediate results. They quickly realized that the FlexCNC was an efficient solution for machining some of their smaller parts. Instead of cutting the parts to size and machining them on a manual mill, they began throwing 300-inch pieces onto the Flex and letting it do its magic.
With a ‘work smarter, not harder’ mentality, they used a piece of channel much larger than their FlexCNC. They drilled the entire bed length, cut the material into 1-7/8″ wide parts, and stuck the undrilled portion back in the Flex to finish the remainder of the piece. H& H found this method was a very efficient way to get holes into parts.
Huff has been impressed with the continual spindle uptime on the FlexCNC. “It is pretty cool with how the open bed design works,” Huff stated, “We have a bunch of vises spaced out about every two feet, and we just stack a part in each vise. You can start on one end, and I just programmed a whole table to be milled. It would start milling the slots, and while it was milling [on one end], I was still putting parts in the other vises. As it gets a couple down, you can jump over to the back side of the machine and start taking off and replacing those parts. So when it’s finished on one end, you can hit start, and it goes back over and starts cutting your other parts. There is not much spindle off time.”
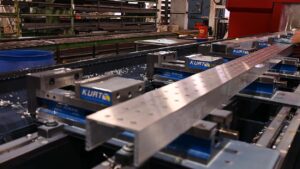
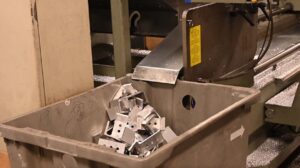
Huff said the Pendulum Mode feature makes for a very tired operator because there is a lot of spindle on time. He compared the FlexCNC to other conventional machining centers saying, “conventional machining centers have a lot of spindle off-time. In fact, there is probably more spindle-off time changing the parts in and out than it is milling the holes. The only time I ever saw the [FlexCNC] stop was when the operator needed a break. The machine was waiting on him.”
“The only time I ever saw the FlexCNC stop was when the operator needed a break. The machine was waiting on him."
Machining Simplicity
A big fear in the CNC machining industry can be operating a machine without previous experience. With the FlexCNC, the operation can be simple and pain-free. With no machining experience, Huff had no problem running the FlexCNC. After taking hands-on training classes with a FlexCNC expert, Huff felt comfortable.
Huff believes that if you have a machine that does G-code, the FlexCNC will be second nature. “I had zero machining experience before those classes. We took a class about an hour and a half long and got hands-on experience in the shop with the product we would be using. I would definitely recommend going to the classes, meeting the people, and seeing how the facility and [everything] operates.”
Increased Productivity
Efficiency and productivity ramped up heavily at H&H Metals with the addition of the FlexCNC machining center. H&H got the opportunity to do a repeat project for a customer. The first time they did it manually, and it took about a week to complete. They recently did the same project with the FlexCNC and finished it in an hour and a half. Huff mentioned, “I almost felt guilty after giving them the bill because why was the first one so expensive? It’s from the standpoint that we found a better way to crack that egg; that’s really what it boils down to.”
Huff explained the reasoning behind their purchase of the FlexCNC and the end goal for their customers. “When we bought this machine, the question wasn’t, what will be the return on our investment? The bigger question was, how do we take care of this customer’s problem and keep them returning?”
"When we bought this machine, the question wasn't, what will be the return on our investment? The bigger question was, how do we take care of this customer's problem and keep them returning?"
Since picking up the FlexCNC, H&H Metals has completely changed its machining processes. Including the ease of producing parts and overall productivity. H&H is an excellent example of what you can do with an efficient and flexible machine tool solution, whether you’re doing large or small parts.
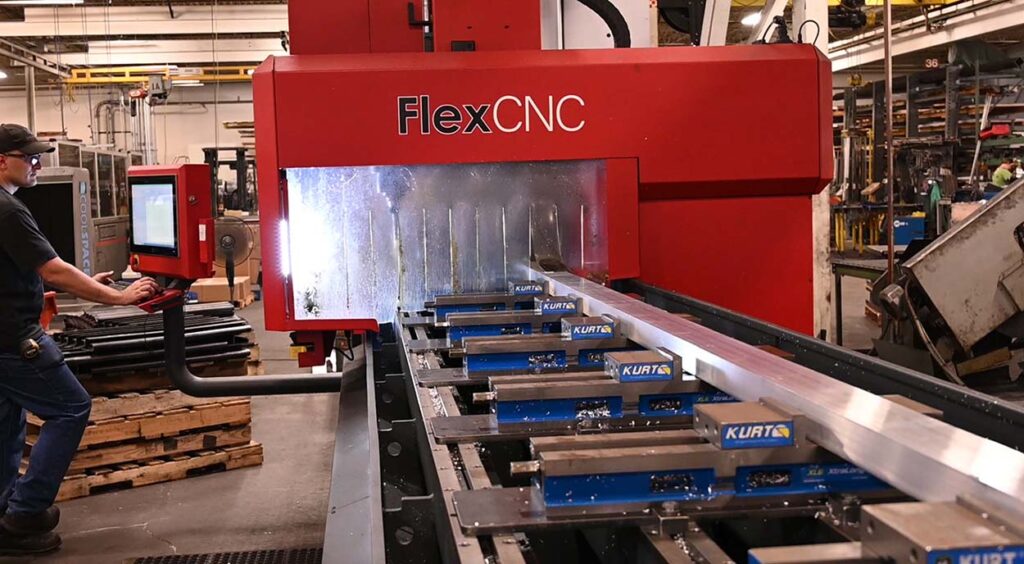
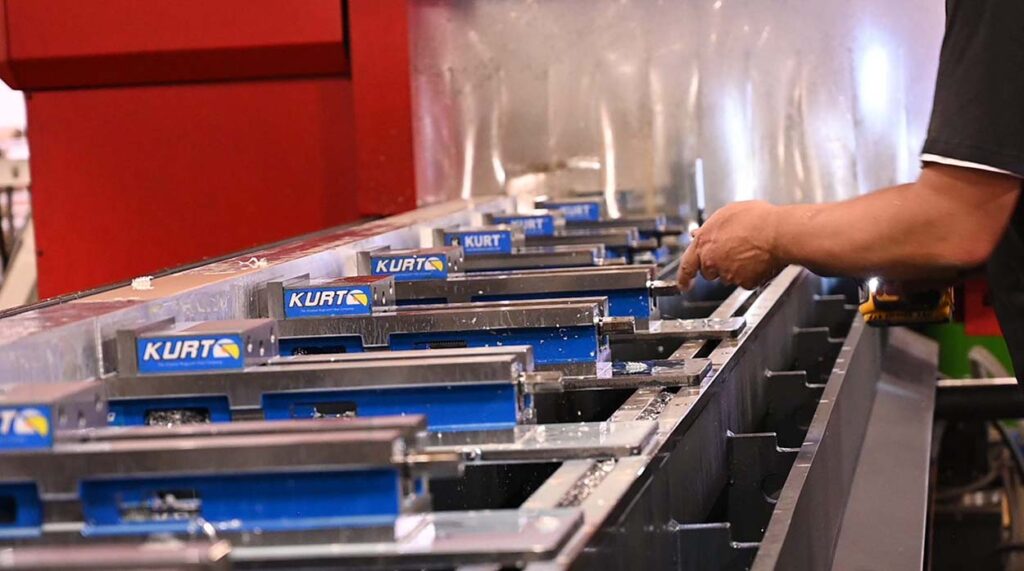
If you want to increase efficiency in your shop, contact us today to see how a FlexCNC can improve your processes. We’d be happy to discuss ways you can improve productivity and keep your customers returning.