WATCH FULL CUSTOMER STORY BELOW
Staying competitive in the ever-changing manufacturing landscape requires continual investments in new technology. Businesses are often looking for solutions that will increase their capacity while giving them the ability to produce more consistent parts safely. Automation has become a hot topic in recent years, and for a good reason. Automating manual processes with a CNC machine often results in faster speeds, increased capacity, reduced downtime, improved safety, and better overall finished parts.
While some businesses are stuck in their ways and are unphased by their demanding manual processes, Viewrail knew there had to be a better way to get the results they were after. By introducing CNC automation, with the help of the FlexCNC Vertical Machining Center, to machine stair stringers, they’ve significantly increased their capacity and have slashed their lead times.
Viewrail designs and builds premium stair and railing systems. Everything is American-made and constructed in-house at their facility in Goshen, Indiana. An extensive range of tubing comes through their facility, requiring different machining processes such as drilling, thermal drilling, milling, or tapping. After searching for a new solution that would fit their needs, Viewrail purchased a FlexCNC C-Series 25-02 in early 2019. The 25-foot long open bed machining center efficiently processes large or extended components. Viewrail knew it was the right machine for the job.
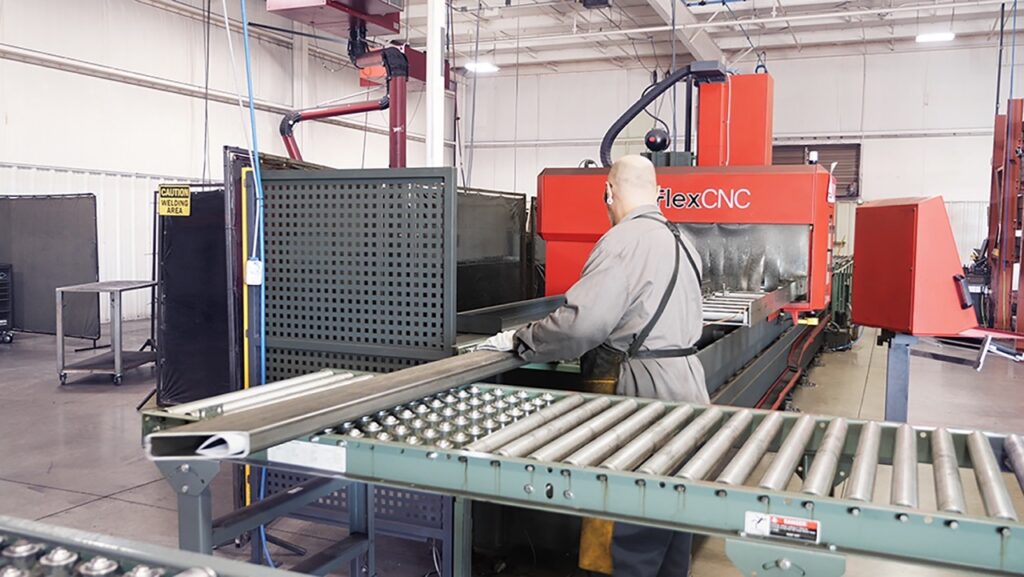
Increasing Capacity and Removing Human Error
Before investing in the FlexCNC, Viewrail manually laid out each stair system pattern with squares and white pencils. Using a Fryer Mill, they would drill a couple of holes and manually move down the length of the tube until the entire 22-foot piece was complete. This highly inefficient process left a lot of room for human error. The FlexCNC automated the whole machining process and helped eliminate any compounding errors they were previously experiencing when machining stair stringers. Now, their tolerances are never questioned, and they have greater confidence in what they are making and sending to their customers.
"We really improved the safety of how we were producing stuff. The operator can step away to work on something else for that 45-minute cycle while the machine runs its work."
After the CNC machine was set up and running, Viewrail saw a three times increase in overall throughput. Graham Morris, the metal production manager at Viewrail, explained that their capacity has significantly grown because they can easily machine everything in one operation, “with that capacity, we slashed our lead times. We went from a 30-day lead time to a 10-day lead time.” Graham also touched on the improvements in employee safety since
automating their process, “We took the human and put the human back into a safe location,” Graham explained, “we really improved the safety of how we were producing stuff. The operator can step away to work on something else for that 45-minute cycle while the machine runs its work.” The FlexCNC, equipped with safety laser scanners, further enhances the operator’s overall safety. If at any point someone breaks the barrier while the machine is running, the spindle will slow down and come to a complete stop before any injuries can occur.
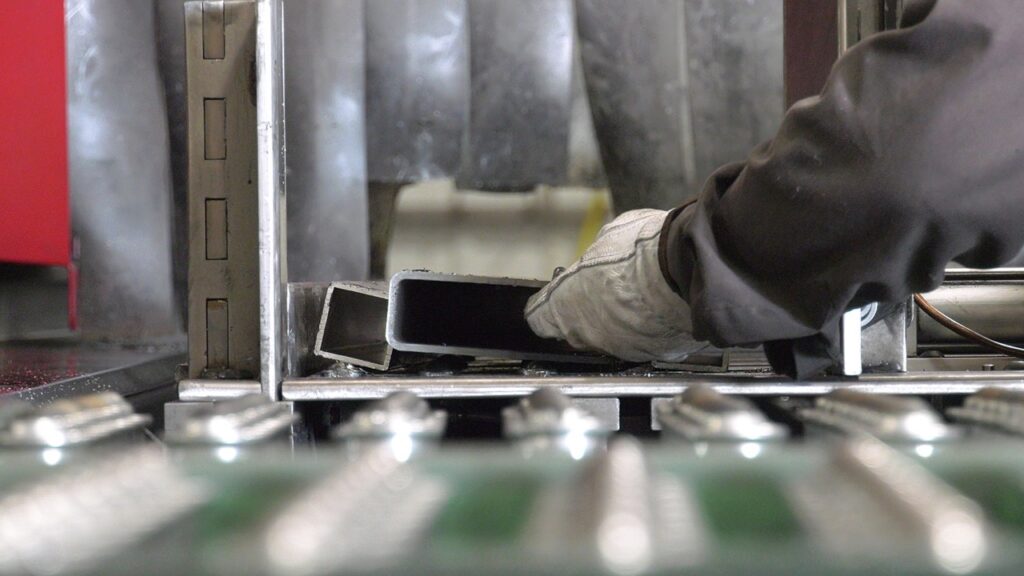
"With that capacity, we slashed our lead times. We went from a 30-day lead time to a 10-day lead time."
The Not So Steep Learning Curve
Going from a manual machining process to a CNC machining process can seem like a daunting task. Some have a preconceived notion that CNC machining has a steep learning curve and that it will take too long to learn how to use them efficiently. Jay Yoder, a machine operator at Viewrail, uses the FlexCNC daily, and at first, he was intimidated by the new machine tool technology. With only two years of experience in machining, he was unsure how long it would take to learn how to operate the FlexCNC. “I’m an older guy. I didn’t grow up with computers,” Jay explained, “so computers are not necessarily intuitive to me. That said, I believe that I’m the type of person that can learn anything with the right amount of training. Within about a half a week, I was running the FlexCNC by myself.”
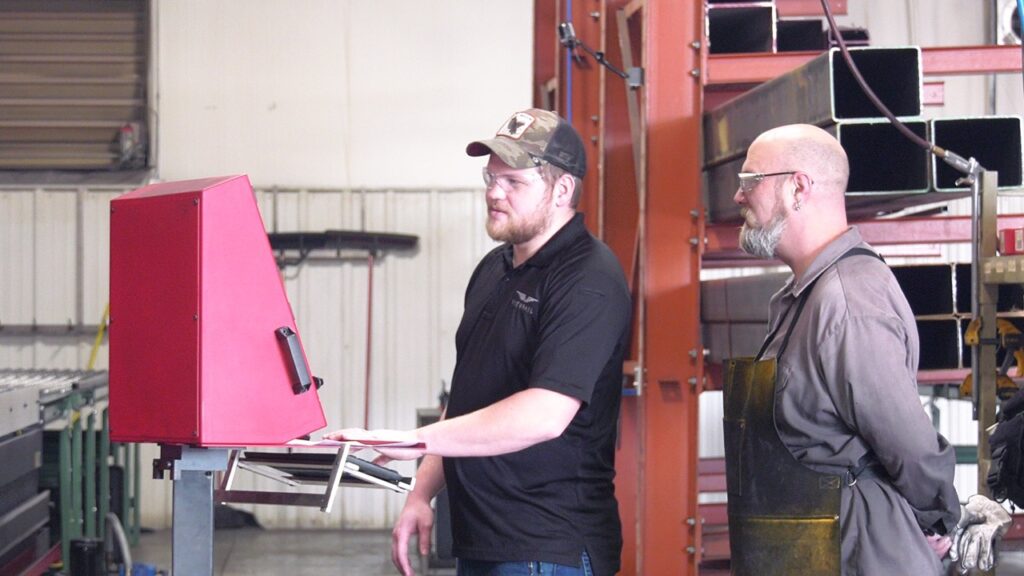
Graham found that operating the FlexCNC was very similar to the Fanuc-based G-code equipment they were already using in their facility. Because the FlexCNC controller is comparable to a Fanuc 31i, it didn’t take long for their employees to get a good understanding of how to operate the machine.
When Efficient Isn't Efficient Enough
To make the job easier and more efficient for its employees, Viewrail equipped their FlexCNC with their own custom fixturing solution with rollers and an automatic clamping system. This solution allowed them to get the long heavy part loaded into the machine with minimal effort. Jay explained that with the efficiency of the machine and the additions of the rollers and fixturing, they can finish the entire 22-foot part in half an hour. “It’s a whole lot easier to move those parts through with the clamps and zero stop,” Jay exclaimed, “I don’t have to fuss and fight with finding my zero. You just put it in, clamp it, and boom, you’re on your way. You don’t have to think about it. It’s set for every single one.”
"Within about a half a week, I was running the FlexCNC by myself."
Since acquiring the FlexCNC, Viewrail has seen significant improvements in its overall manufacturing process. From improved employee safety to increased capacity and throughput, Viewrail is reaping the benefits by offering their customers shorter lead times and exceptional quality products.
If you are looking for a more efficient solution and are interested in automating your process with a FlexCNC, contact us today. We would be happy to discuss how we can help you increase throughput and earn larger profits.