Processing Long Pipe & Tube with FlexCNC
The old saying “Time is money and money is time” has special truth at a machining facility. Plant managers and manufacturing engineers endlessly scrutinize tools and processes in search of laborious tasks that can be sped up without reducing safety or part quality. At a multiple-shift plant, saving seconds in a recurring task adds up to profound productivity over the course of a day.
Many plants seem to have a time vacuum that sucks up precious labor hours, such as when an operator has to change vises or set up the next job. But Felker Bros. Corp.’s Marshfield, Wisconsin, plant struck time-saving gold when it replaced a machining center.
For more than 100 years, Felker Bros. has manufactured fabricated and custom piping products for a variety of industries, including wastewater treatment. The company’s plants in Marshfield and Plover, Wisconsin, and Glasgow, Kentucky, see an incredible range of pipe sizes and materials with different drilling needs every day, which puts a strain on Felker Bros.’ drilling and deburring processes.
The company had been using a drill press on a linear system and would

contract out large jobs to a shop with a pipe laser system. Buying a pipe laser was cost-prohibitive, and plasma cutting didn’t provide the needed quality and left dross buildup that required cleaning. So Felker Bros. turned to CNC machining.
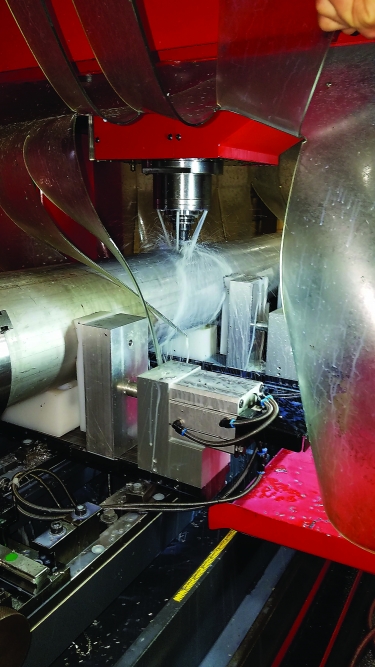
Josh Bohman, a member of the product development committee, came across machines from FlexCNC, Wapakoneta, Ohio, by searching the internet. After Felker Bros. determined the total cost of the project and requirements for plant layout, site prep, installation and workflow, Plant Manager Jim Kluball purchased a C-Series 35-02. The 35′-long open-bed milling machine efficiently processes large or long components. The equipment was ordered in December 2017 and installed in June 2018.
Previously, with its drill press, Felker Bros. followed a multiple-stage process in which an operator would mark and manually drill holes, slide the pipe through a fixture to the next position, clamp it and repeat the process position to position throughout the entire pipe length while making sure that everything was perfectly level and in line. Profiling was done on vertical CNC mills.
The C-Series 35-02, however, drills, mills, taps and bevels in one setup. As a bonus, the manufacturer eliminated a machining center, as the new machine does the work of multiple machining centers.
Now, someone programs a part and sends the program to the machine. An operator sets the pipe inside the machine with the proper fixturing and calls up the program. Whether it’s one hole or 30, the open-bed mill does the heavy drilling. A fourth axis rotates to handle profiled or other holes on some of Felker Bros.’ most difficult parts with 180° rotation from the original holes. The operator deburrs the pipe before removing it and replacing it with a new pipe for drilling.
Though the team was relatively fresh to the CNC world, it found the new equipment easy to operate, and the learning curve was lessened by training at FlexCNC.
“The major challenge was designing the correct fixtures to secure the pipe, making changeover quick and using the correct tooling,” said Don Pannhoff, manufacturing engineer at Felker Bros. “Programming is easy and G code-friendly.”
The plant handles pipes from 3″ to 14″ in diameter and up to 35′ long. The majority of the stainless steel pipes are 4″ in diameter and 21′ long and require 5⁄8″ to 7⁄8″ holes. Felker Bros. estimated that when it drills 5⁄8″ holes every 8″ in 4″-dia. pipe for a 21′ length, drilling time is reduced 50 percent compared with the previous method.
In addition to saving time and increasing sales, hole and hole location accuracy are higher than with the manual process. Demands and parts vary from day to day, but saving half the time it previously took to drill a pipe could equal drilling twice as much pipe each day.
In the past, errors in layout would result in cutting out a section and splicing or butt welding a new piece of pipe. This consumed extra material and could potentially cause a shipping date to be missed.
An added advantage of the new machine came at the end of pipes. Whereas laser cutting required an extra foot of pipe to grab the piece and rotate it, the FlexCNC machine can rotate the part as is, saving a customer from paying for extra stock, which ends up as waste.
By combining multiple steps into one process, the machining center handles some of the most challenging parts faster. Every second saved adds up to hours over the course of a day—and saving time while increasing productivity and accuracy is a no-brainer for Felker Bros.