A prospect out of Monroe North Carolina reached out to FlexArm because they were looking for an alternative tapping method that would eliminate tap breakage. The end-user taps into 4140 pre-hardened steel as well as a variety of other alloy steels. They were tired of breaking taps so they sent in some of their parts to see if the FlexArm could help prolong their tool life.
Three different sized taps (10-24, 5/16”-18, and 1/2”-13 ) were used to thread 1” deep blind holes in the 4140 steel. To accommodate the 1/2”-13 tap, the RNR-20 pneumatic arm and GH-18 hydraulic arm were chosen to show the end-user the speed difference between the two arms. The RNR-20 in low gear is limited to 100 RPM, but the GH-18 has a speed governor in the power pack, allowing the user to fine-tune their speeds. Therefore,
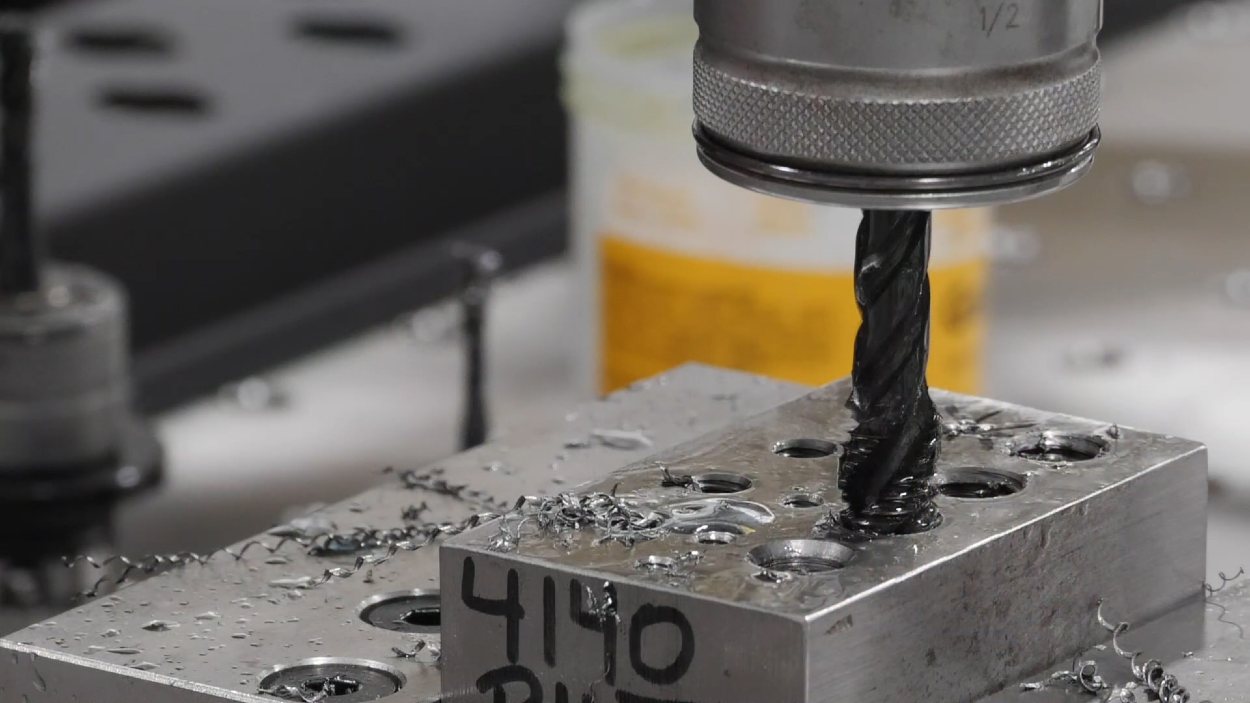
the GH-18 can thread the 1/2”-13 tap faster at 200 RPM. Testing the material with both arms gave the end-user the opportunity to see how each arm would perform on their parts.
If you have a similar application where you are tapping into alloy steel or just looking to speed up your tapping process, contact us for a quote or schedule a tap test today.
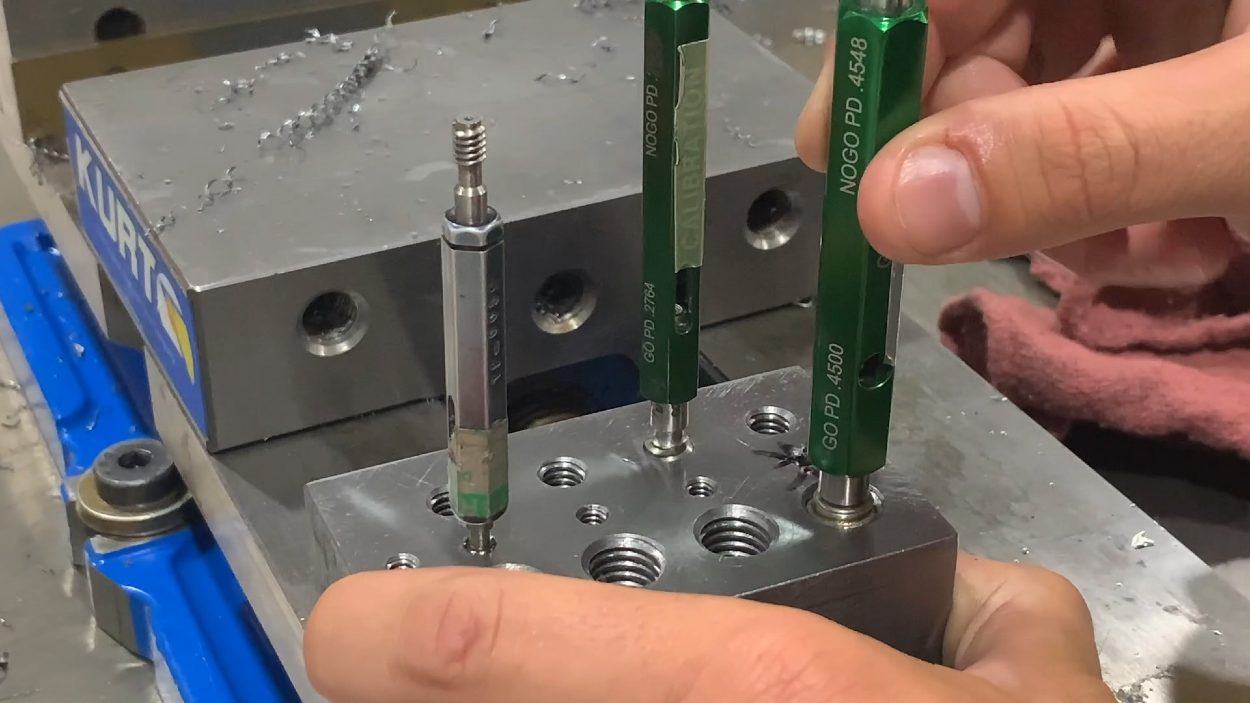