Petty Welding is a fabrication shop in Knoxville, Tennessee, that focuses on welding, fabrication, custom-iron work, and on-site repair. They’ve been in business for 11 years, and their workload has been steadily increasing since then. With any fabrication work comes grinding work. This repetitive, monotonous task started taking a toll on the employees of Petty Welding. However, the addition of a FlexArm Balance Arm has helped decrease repetitive motion injuries caused by their grinding tools. Read about their story and experience using the FlexArm B-33-RG Balance Arm.
This interview has been edited and condensed. See the whole interview in the video here.
PETTY WELDING
Andrew Petty was born and raised in Sevierville, Tennessee. He moved to Knoxville, Tennessee, and started Petty Welding 11 years ago. Andrew knew he would never fit into anyone’s mold, so he decided to create his own mold by starting Petty Welding in the spring of 2010. There has always been an immense amount of production work in East Tennessee. According to Andrew, “it’s always booming all the time.” “We don’t care if there’s a recession, we don’t care if there’s a pandemic,” said Andrew. “There’s work here all the time. We only got busier in 2020. It was our best year ever, and we only got busier. We never missed an hour’s worth of work last year.”
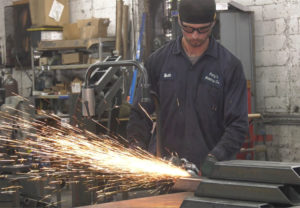
Petty welding started in heavy equipment but has grown and morphed into the fabrication jobs they do now. They still have the heavy equipment wing, but they also do a lot of shop fabrication, shop CNC work, and plasma cutting.
Greg Bull is the Shop Welder at Petty Welding. He and Andrew met in a welding class at the local community college. Greg was very green trying to get his career started when he first met Andrew. They spent a lot of time talking about the welding trade and how to get involved in it. Eventually, Andrew decided to let Greg start working with him.
THE WOES OF GRINDING
Grinding with an angle grinder on a heavy plate year after year for hours on end can have detrimental effects on the end-user. Andrew explained, “I got to the point where I destroyed my wrist, so carpel tunnel set it. I was losing sleep every night. This stuff is stressful enough and hard enough on your body. If you’re not resting well, you’re going to be destroyed.” Andrew has spent enough time in the trade to know what these tools can do to one’s body, and he’s always looking for better and smarter ways of doing things. Since acquiring the FlexArm B-33-RG Balance Arm, it has become an essential tool in their shop. “I’m a big fan of the FlexArm,” said Andrew. “It takes some of the monotonous, boring work in production metalwork and makes it easier on the end-user. It doesn’t do anyone any good to kill your employees, wear them out, and expect them to perform day in and day out, and if you don’t care about that, you shouldn’t be in management.”
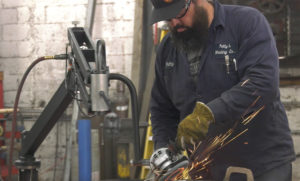
Greg is also no stranger to the angle grinder. He spends more hours grinding in the shop than he does on any other process. “The grinding starts wearing in your fingertips,” said Greg. “You can feel it in your hands, wrists, and even your shoulders just from bearing down on the grinder and feel that weight. There have been days where I’ve ground nonstop for days on end, and you feel it every day.”
A BETTER SOLUTION
Greg says the FlexArm changed everything about grinding for him. He dreaded going to the grinder before the FlexArm balance arm, but now he enjoys it. He can go home and do the things he enjoys doing without thinking about his wrist hurting and having to take a pain reliever. Greg feels better all around. “I think it’s worth investing into your personal health and your body,” Greg said, “I think the FlexArm is a smart investment overall for someone to have in their shop if they want longevity out of their career. If you want to continue doing what you love, then it’s the investment to make.”
If you’re experiencing pain and injury from repeated grinder use, the B-33-RG Balance Arm may be the right solution for you. Contact us to request a quote.
Read more about the B-33-RG Balance Arm here.