Watch the video of this time study at the bottom of the page
Using a CNC Machining Center to drill is safer, faster, and more accurate than other traditional drilling methods. Drilling with a machining center helps reduce the margin of error because the operator performs a minimal amount of hands-on work. A CNC machine can dramatically improve cycle times when paired with the proper tooling.
In the past, we ran a time study where we tested the FlexCNC Vertical Machining Center vs. a Fosdik Radial Drill (watch it here). The FlexCNC was able to drill faster and accomplish much more in 5 minutes than the Fosdick. Since shops are always looking for ways to speed up production, we decided to test two drills to see if one could perform the job faster than the other.
We ran the test on two different Allied Machine & Engineering drills. Both are great drills, but we wanted to test cycle times and the quality of each hole. The test involved the GEN3SYS XT Pro Insert Drill and the 4TEX IC Drill. Both drills are 1.343” in diameter, drilling a hole 2.00” deep in 1018 cold-rolled steel.
Results
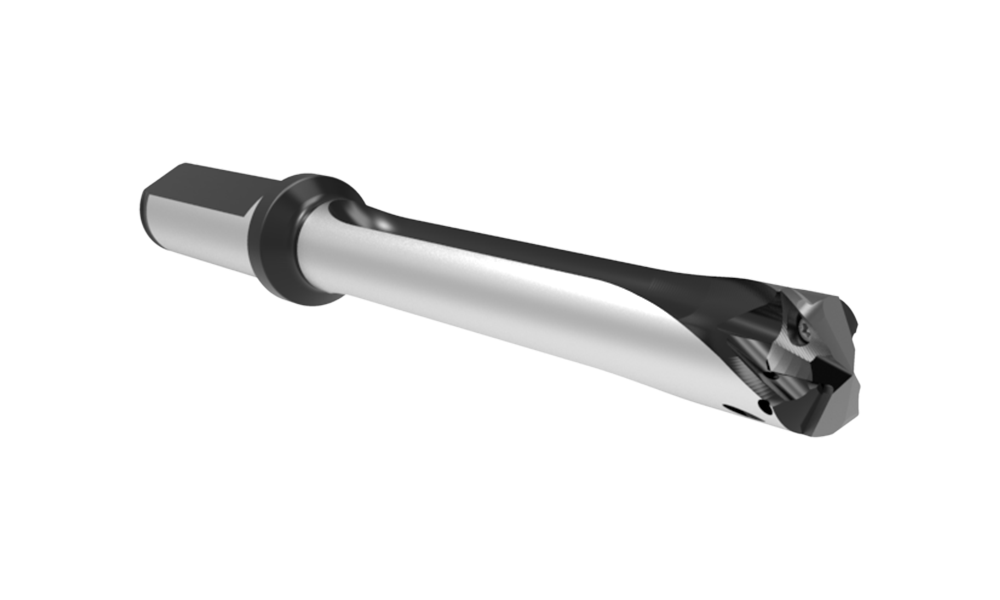
GEN3SYS XT Pro
400 SFM (1137 RPM)
.016 IPR (18.3 IPM)
8.5 Seconds per hole
45 Second Cycle time
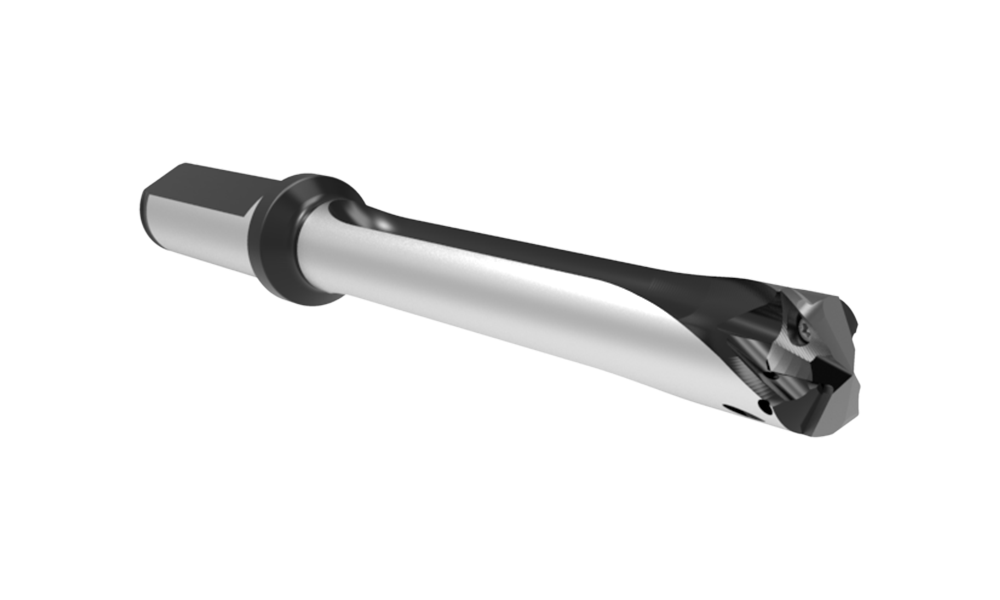
4TEX
800 SFM (2275 RPM)
.0032 IPR (7.3 IPM)
20 Seconds per hole
1 min 4 Sec Cycle time
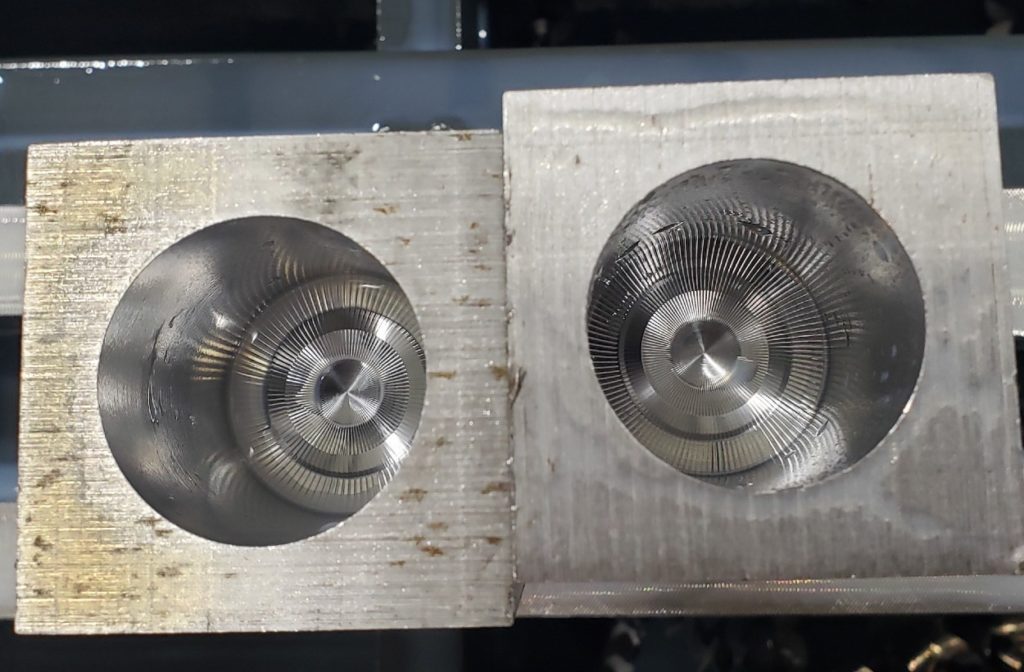
4TEX
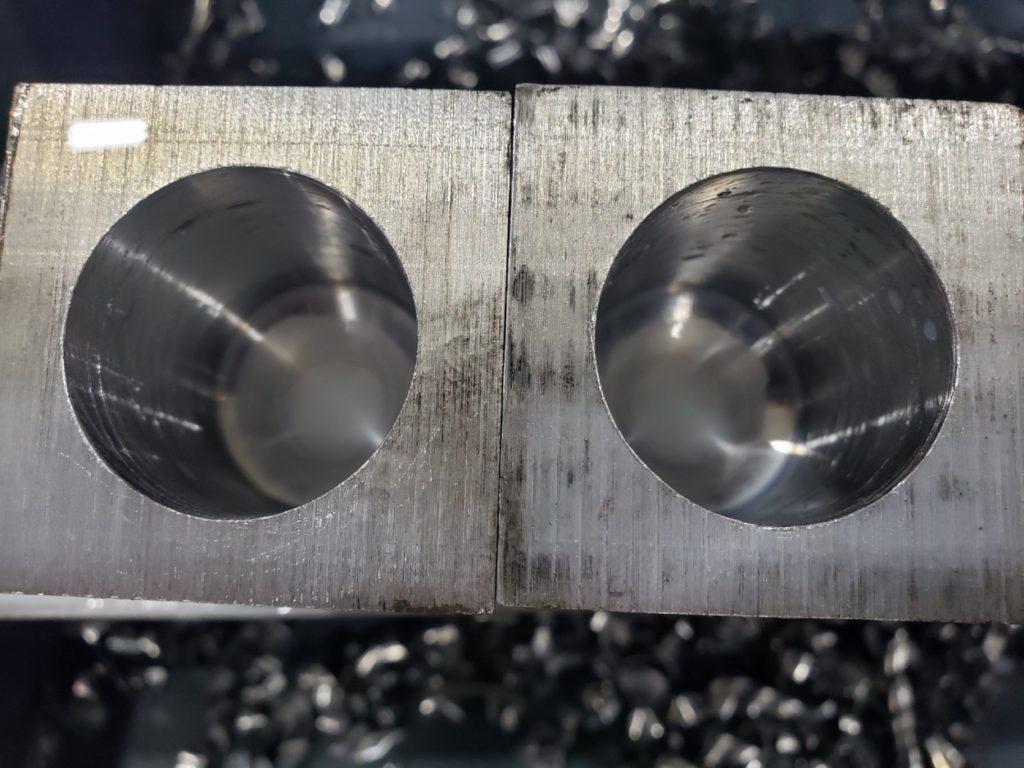
GEN3SYS XT Pro
The drilling process can be tedious and time-consuming. Fab shops with long or large parts spend too much time on each piece; the added refixturing time makes the drilling process entirely too long. Whether you’re using mag drills, gang drills, or radial drills, a switch to the FlexCNC can increase cycle times and save shops significant amounts of time and money in the long run.