Waterjet cutting is a manufacturing process that uses highly pressurized water, sometimes with an abrasive, for an accelerated eroding process that can cut and shape a wide range of materials. Waterjets are quickly rising in the industry as one of the top machines for cutting due to their flexibility, precision, edge finishes, eco-friendliness, and more. Here is a detailed guide on waterjets to help you decide how waterjet cutting will benefit your business.
How does a waterjet work?
1. Generating Pressure
The specialized pump system generates pressure to move the water into the machine. With a FlexJet, that pressure can measure up to 90,000 PSI. For reference, atmospheric pressure, or the force of air pushing down on Earth, is only 14.7 PSI at sea level. This amplified water is fed through stainless steel high-pressure tubing into the cutting head, which will further increase its velocity for fast, efficient cutting.
2. Going Through the Orifice
Water is tapered into the orifice, which returns lost velocity to the water after traveling from the pump to the head. The orifice is a small chip with a small hole in the center, most commonly made of synthetic corundum, a material only surpassed in hardness by diamond. These orifices are divided into categories, each affecting the water stream differently. FlexJets offers the orifices in diamond and sapphire, both of which guarantee longevity under care.
3) The Venturi Effect
The Venturi effect is the drop in pressure as fluid flows through a constricted area of a pipe. As pressure drops, fluid velocity increases. The hole in the orifice is thinner than a human hair, which creates a vacuum that adds velocity and makes the stream more powerful and precise.
4) Introducing an Abrasive
Depending on the waterjet’s function, there are two options: pure water and abrasive. Pure water is just that; if a material can be cut with a knife or scissors, water by itself will cut it. If the material is sturdier, an abrasive is introduced to optimize the erosion process. The standard abrasive is garnet, which is not only abundant on the Earth’s surface but recyclable. Flexjets offer both abrasive and water-only options.
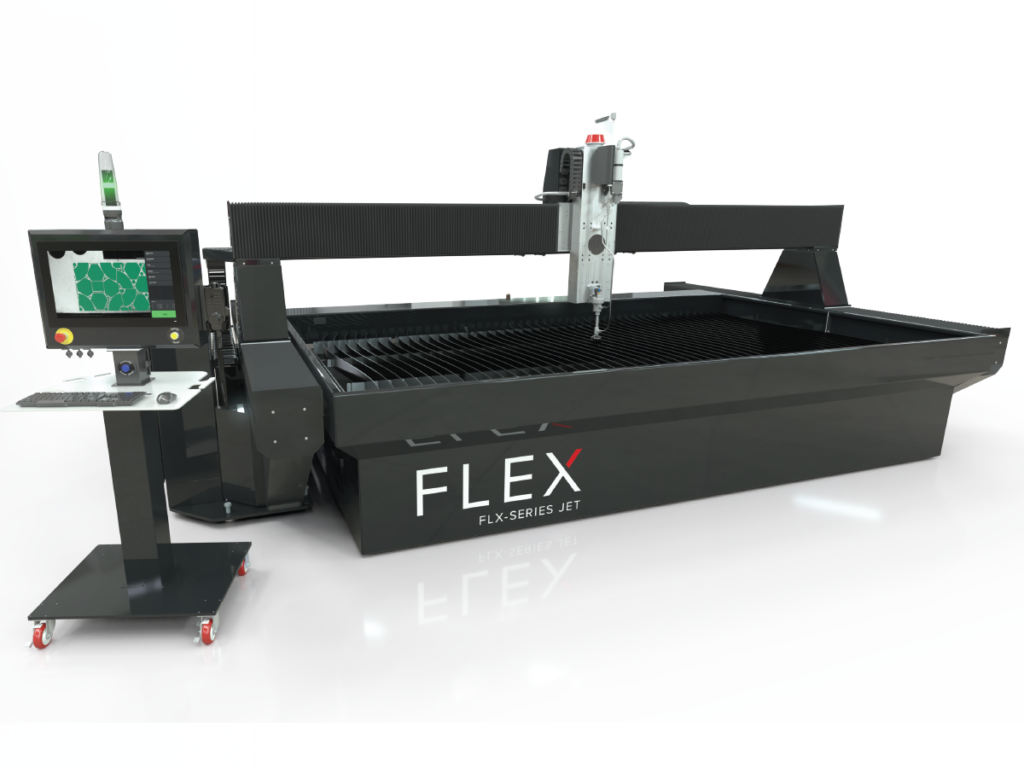
5) Cutting Heads
The type of cutting head will generally depend on the nature of the project. FlexJet offers three different options for the cutting head: conventional, tilter, and 5-axis. The conventional cutting head is for 2D cutting at an angle of ±0°, while the tilter and 5-axis cut at ±45° and ±70°, respectively, for taper compensation on complex geometries. Each cutting head is specialized for the project, depending on how the material is cut.
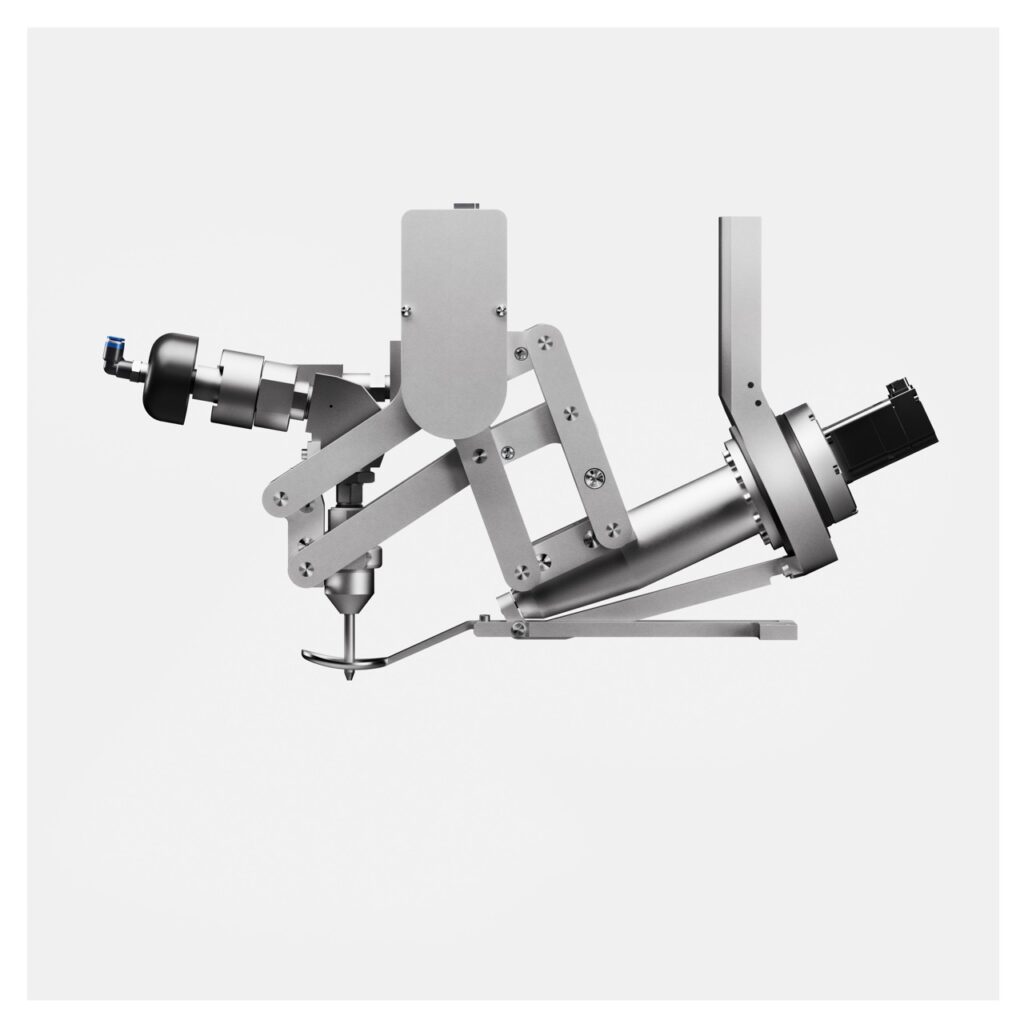
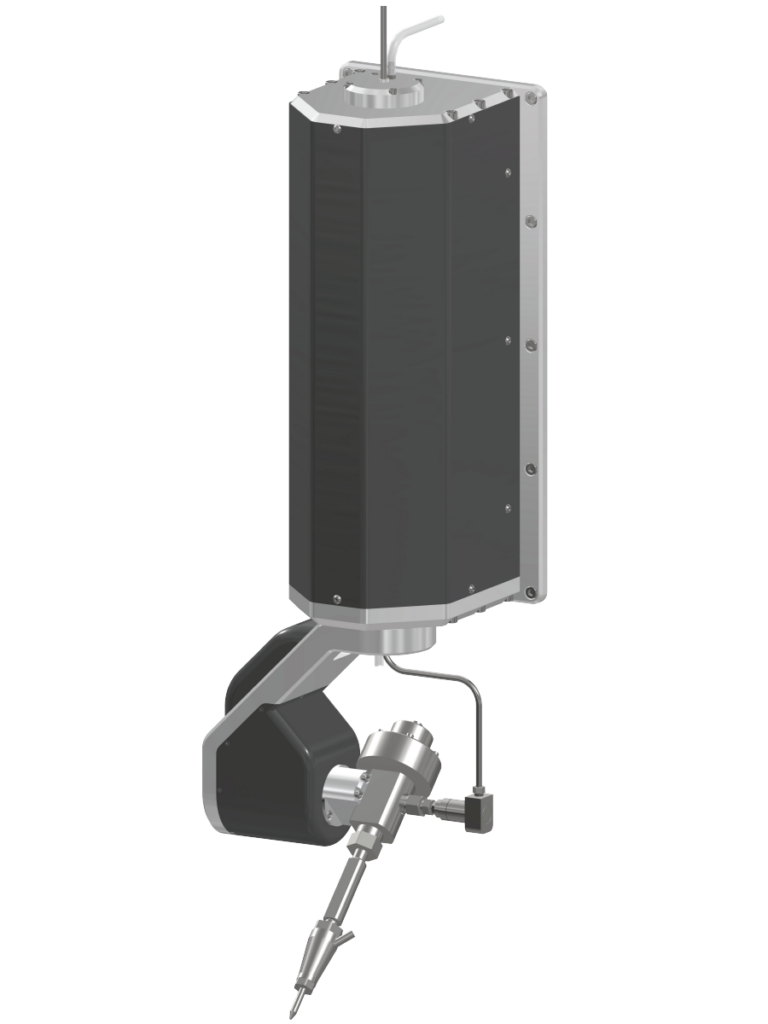
6) Cutting the Material
Water and abrasive are shot out of the nozzle to begin a powerful eroding process. The processing time will depend on the material and the project; however, FlexJets are built with speed in mind, moving at a maximum speed of 1,800 inches per minute. Afterward, you will be left with highly precise and smooth-edged cuts.
What are some benefits of waterjet cutting compared to other methods?
After learning the process of a waterjet, you may be wondering how it stacks up against laser, plasma, wire EDM, and other cutting methods. Here’s how a waterjet surpasses the competition:
Cold Cutting
Most cutting processes generate heat, which leaves a heat-affected zone on the edges of the part. While this does not lead to melting, it does lead to a change in the material’s properties. Discoloration, heat distortion, and hardened edges can all affect the characteristics of the final part, which will require heat treatment before being put into use.
Waterjet cutting, on the other hand, is a cold process. This means there is no need for secondary treatments and no worry about imperfect cuts, weak points, warping, and flaws, which can affect the product even after it has been sold. Less waste is created with fewer broken parts. Additionally, waterjet cutting leaves smooth, velvety edges that do not require a secondary process to finish.
High Accuracy
Waterjet cutting is highly precise and produces quality products even with tight restrictions. Tolerances can range from 0.075 to 0.125mm for parts less than one inch thick. The accuracy depends on factors such as table stability, machine construction, abrasive flow rate, cutting stream control, stream lag, and process error.
Sustainability
Waterjets use less energy, produce no hazardous waste, use recyclable materials, and avoid using coolants and lubricants. They are highly cost-effective, with the ability to cut multiple parts or materials in one go and, again, need no secondary processing. For more information about the environmental impact of waterjet cutting, read it here (environmental article).
Compatibility with Different Materials
With suitable parameters and abrasives, waterjet cutting can tackle a broader range of materials than any of the alternative methods. For industries dealing with multiple materials, this makes a waterjet ideal for its flexibility and efficiency.
What are Some Practical Uses for a Waterjet?
You may be wondering how waterjet cutting is applied by real industries.Waterjet cutting is widely used in various industries for efficient cutting. The following are some of the practical application cases of a waterjet:
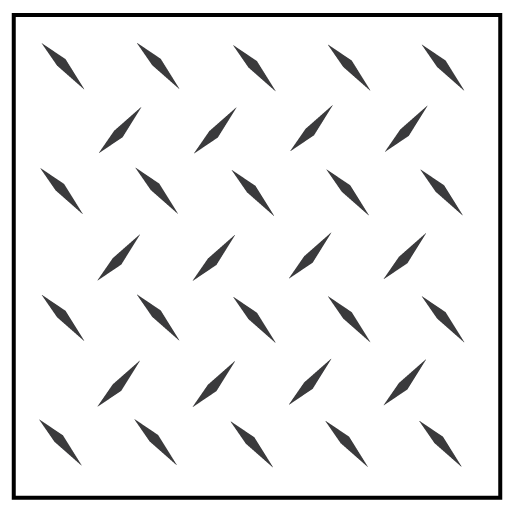
Cutting Metal
Water jet technology can cut any metal, including titanium, brass, copper, hardened tool steel, aluminum, and other unusual metals. As mentioned before, since water jet cutting does not raise the temperature of the workpiece, its structural and chemical integrity is not compromised, making it very useful in industries where multiple types of metal are needed or the integrity of the part is essential.
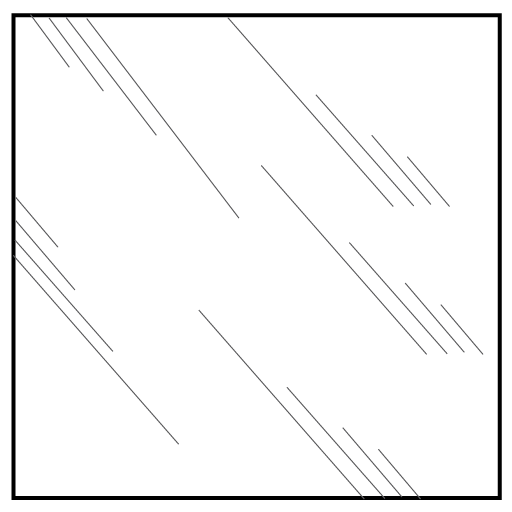
Glass
Cutting glass using traditional methods can cause it to break quickly because they apply more stress to the fragile glass. The waterjet stream only applies pressure where the cut is occurring, meaning most glasses will not shatter with waterjet cutting. This makes it a preferred cutting method in glass industries.
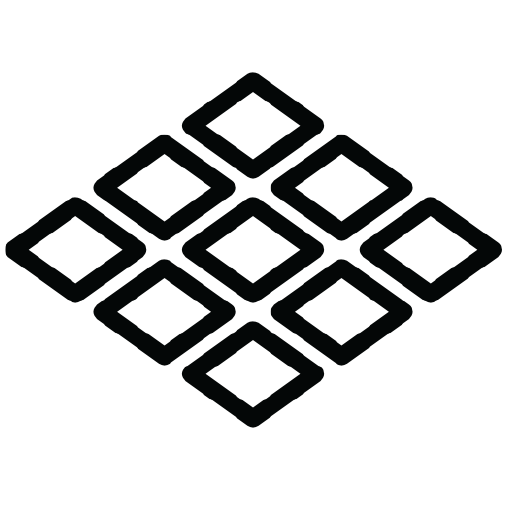
Stone & Tile
Granite, marble, porcelain, stone, and tiles can all be precisely cut using abrasives added to jet-cutting equipment. Waterjet cutting can cut through all types of stone, soft, hard, or brittle, up to 11” thick. It is especially helpful for easily breakable mediums such as porcelain, and it effortlessly cuts bevels.
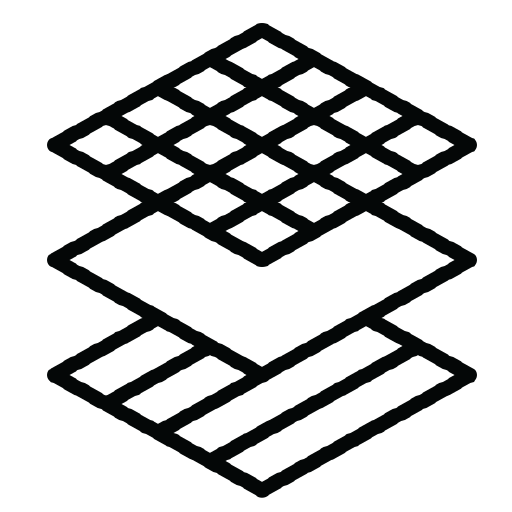
Plastics
The use of high-temperature tools on plastics releases hazardous gases. As mentioned, water jet cutting is the safest method for cutting polymers because there is no temperature increase during the process. There is also no chance of melting the plastic, ensuring a consistent, uniform cut edge around the part.
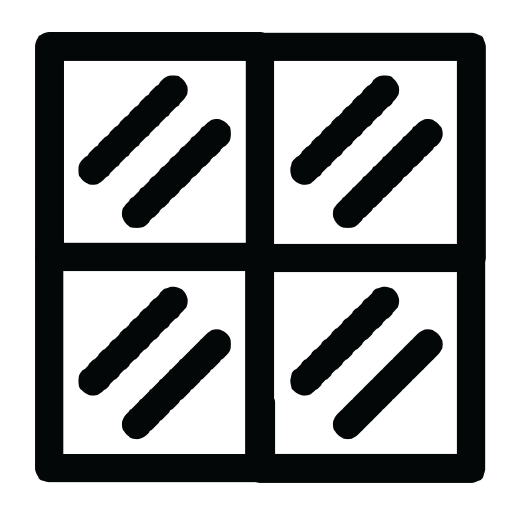
Ceramics
Ceramics require costly saw blades and are difficult to manufacture due to their lack of durability. Some ceramics can be significantly harder than steel, making them one of the most challenging materials to cut. For this reason, water jet cutting proves to be a less expensive and easiest cutting method for ceramics.
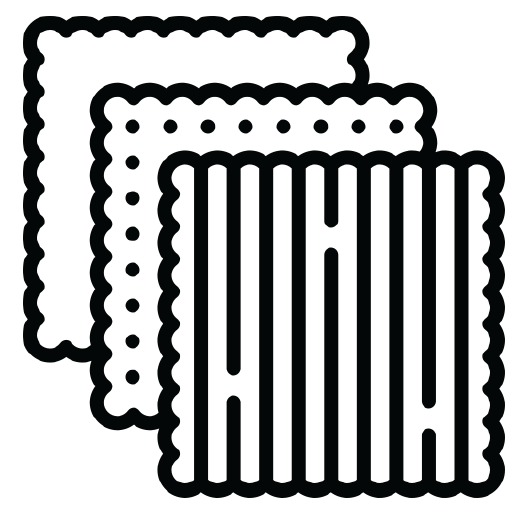
Textiles
Water jet cutting is exceptionally gentle on the fabric, making it an ideal choice for delicate or heat-sensitive materials. There is no physical contact with the fabric, and minimal force is applied, which ensures that the fabric’s properties, such as weave and texture, remain unaltered.
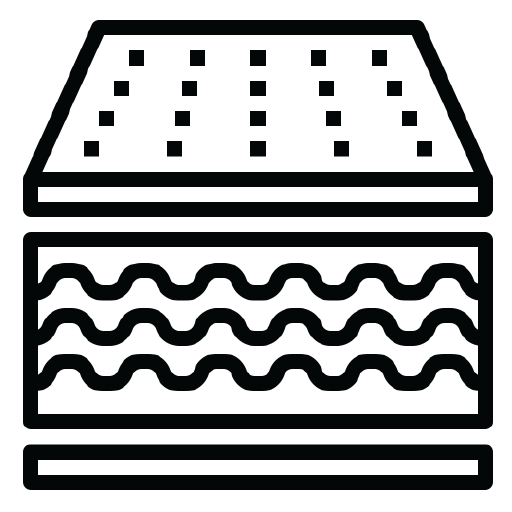
Rubber and Foam
Rubber emits harmful gases at high temperatures, similar to plastic. Due to waterjets not producing heat, it is a great safety measure that manufacturers all over the globe utilize to make rubber and foam parts.
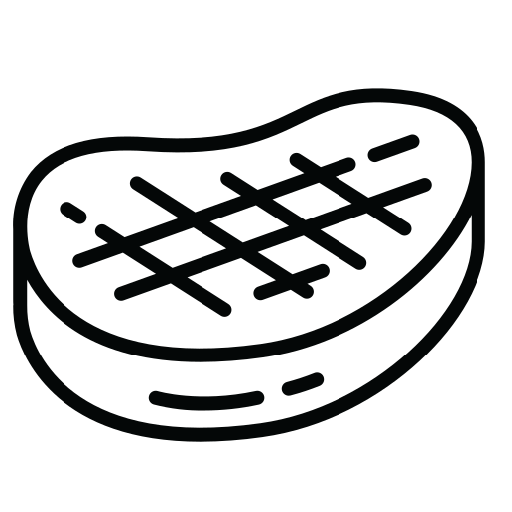
Food Processing
Pure waterjet cutting is a USDA-approved method that offers many productivity and sanitation advantages over other cutting methods. With no blade or metal cutting, there is no bacterial transfer from food to food and no downtime for sharpening. The cut quality is exceptionally high, with a clean edge free of smearing or tearing.
Conclusion
Waterjet cutting is an efficient and optimal process for many industries and ranks high above the competition. FlexJets have been used in many industries for many different parts, materials, and purposes. If you are ready to upgrade your business, contact us today for a free quote on a FlexJet waterjet.