Watch the video of this application at the bottom of this page.
We had an end-user out of California interested in seeing if the FlexArm could handle their tapping needs. They are a manufacturer that deals with a lot of R&D, so they needed an arm that could tap a wide array of parts and materials. We chose our largest tapping arm, the GH-60, because we needed to tap multiple 1 1/4″ holes in heat-treated alloy steel. We also added the multi-position head to allow the capability of tapping horizontally (and any angle in between) in addition to the typical vertical position.
The end-user was hoping the FlexArm would be a fast alternative to their current time-consuming tapping process. They tried tapping the holes in their expensive machine, but it was unable to completely reach the bottom, so they are spending
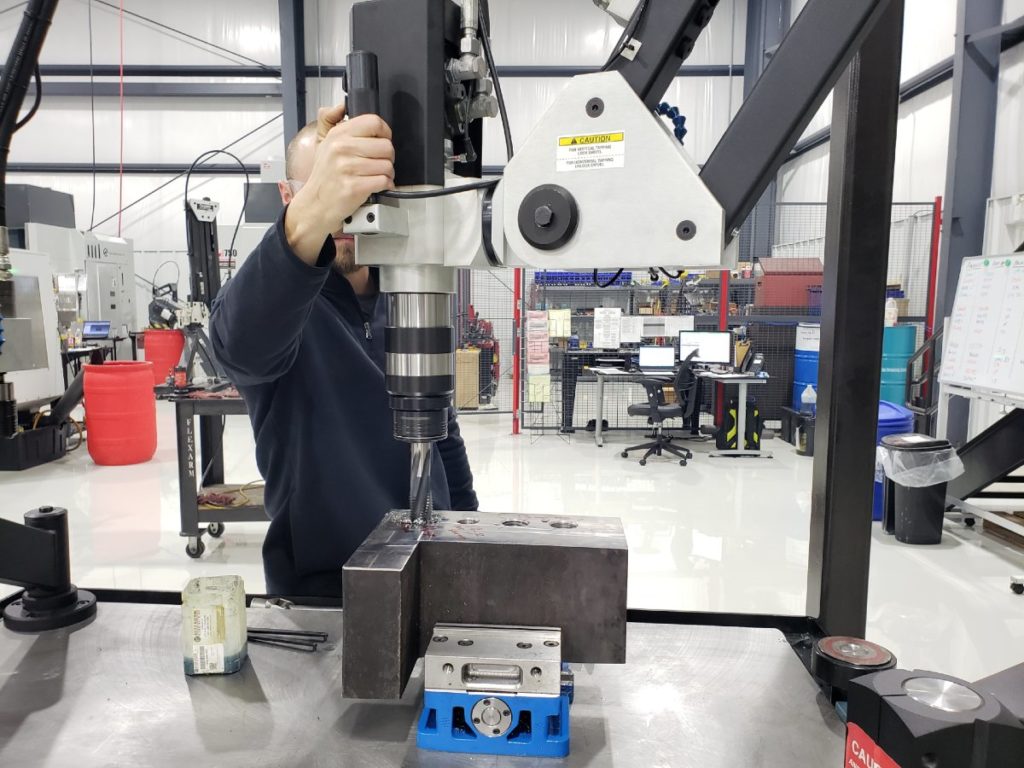
a lot of time trying to finish out these holes. The FlexArm had no trouble tapping the hardened alloy steel, and we were able to show them just how fast and easy their tapping process could be with our turnkey solution.
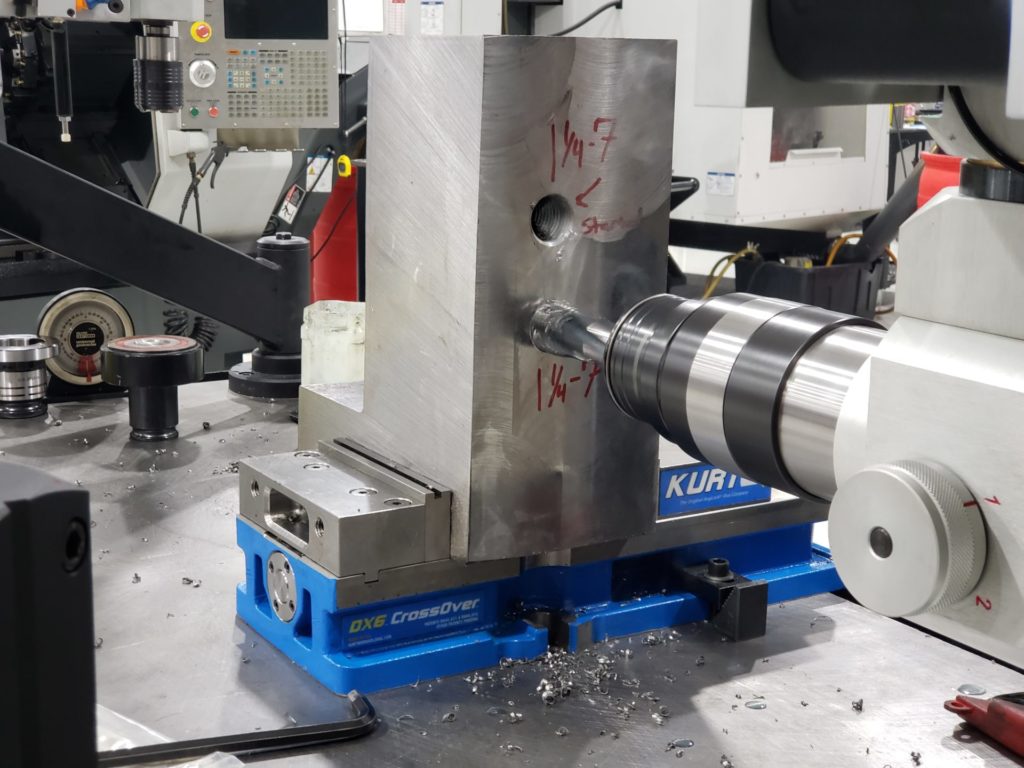