An end user recently approached Flex facing a common challenge: tapping plasma cut holes in A36 Steel. This particular end user is a general fabrication shop that handles a wide variety of projects but is well known for its expertise in fabricating truck beds. As a result, they frequently need to tap holes that come off a plasma or waterjet cutting system, which often requires a secondary tapping operation.
After experiencing the benefits of borrowing a FlexArm from a neighboring shop, the end user realized it was time to invest in one for their operations. The unit they borrowed was an old pneumatic tapping arm, but they were interested in seeing how an electric FlexArm would perform. The convenience of plugging the unit into a standard 110V outlet and immediately start tapping was appealing. Here’s what they tested
The Electric Tapping Arm Test
•REM-16D Electric Tapping Arm
•Tapping plasma cut holes with M5, M6, M8 taps into 1/4″ A36 Steel
•Tapping plasma cut holes with a M12 tap into 1/2″ A36 Steel
•Tapping plasma cut holes with an M8 into 1″ A36 Steel
We demonstrated the electric tapping and its ability to handle plasma cut holes. We also exhibited the usefulness of using the programmable depth stop for through holes. With this feature, the operator can tap without any worries. Once the operator aligns the tap with the hole, they just need to push a button. The tap automatically drives to the correct depth and then backs itself. If you do production runs, this is a handy feature to have.
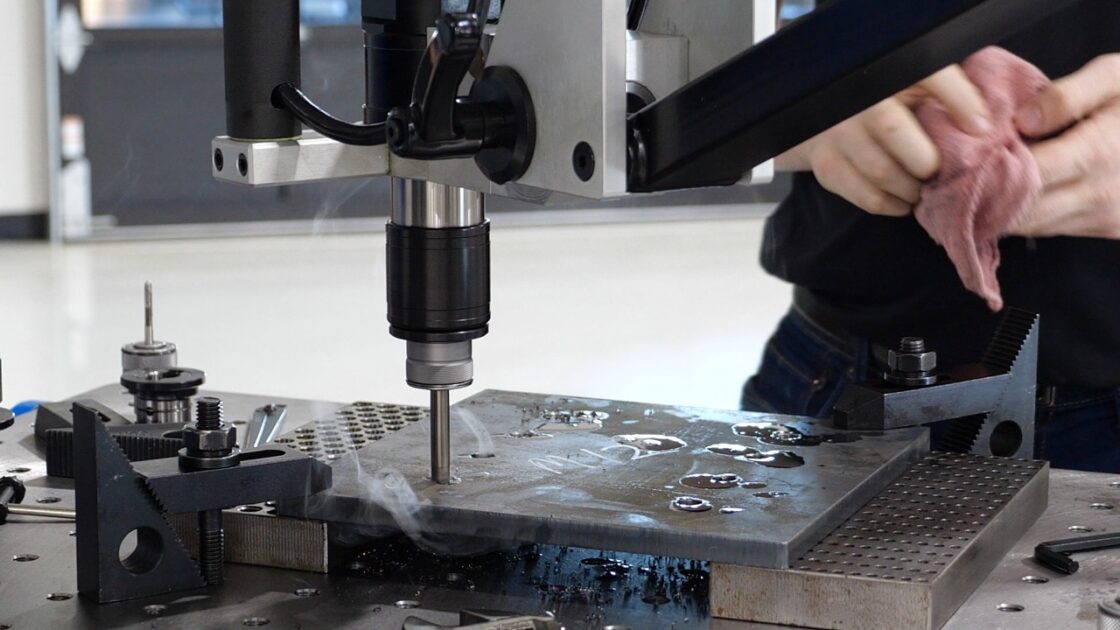
Overcoming Misshaped Holes and Heat-Affected Edges with FlexArm
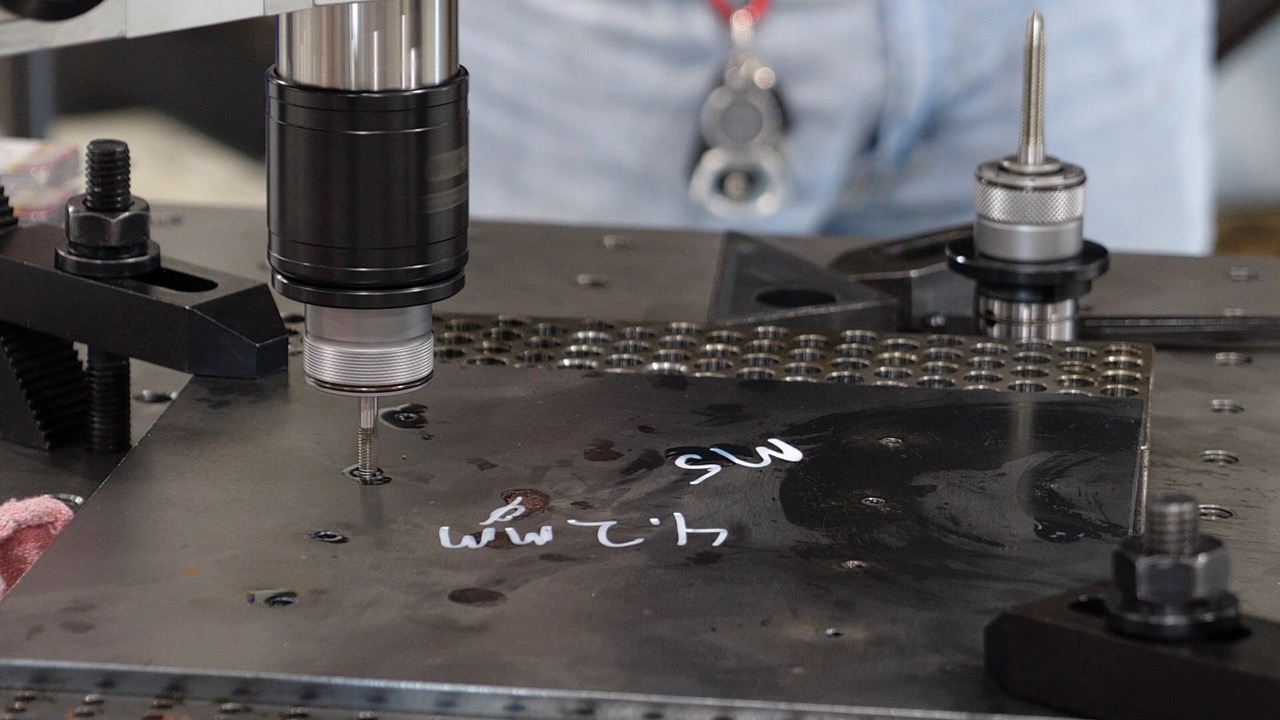
One concern often associated with plasma cut holes is the potential for misshaped holes or the heat-affected edge. This makes tapping plasma cut holes difficult even with a high-quality tapping machine. However, with the FlexArm, tapping plasma cut holes should not be a problem, provided you use a new high-quality tap (We recommend OSG taps) and take certain precautions. For example, some people find it helpful to run a reamer through the holes first to extend the life of
the tap. The FlexArm can easiliy accommodate this by placing the reamer into the quick-change drill chuck and using the arm as you would for tapping. Dropping the RPMs can also help to break through the hardened edge.
If you are having issues tapping holes coming off your plasma table. Send in your parts. We would be happy to conduct a tap test and Demonstrate the value of a FlexArm tapping system.