March, 2025- With a business model based on the aspiration to do everything from project concept to implementation, Fulcrum Technologies Inc. wanted to become more vertically integrated and added more in-house processing to its list of capabilities, says Craig Johnson, director of plant operations. That list includes design, engineering, testing, installation, welding, heat treating, powder coating and concrete. The company specializes in manufacturing high-performance pedestals for machines used by makers of computer chips, as well as producing an array of components used in these facilities.
Fulcrum has two facilities in Oregon one in Tualatin and the other in Lake Oswego to create its projects end to end and has install offices around its key customers.
To increase its capabilities, Fulcrum invested in a 6 kW fiber laser, press brake and gantry-style machining center, Johnson says. In addition, Fulcrum purchased a FlexJet FLX-1365 abrasive waterjet machine with a 5-axis cutting head from Flex Machine Tools in Wapakoneta, Ohio. Fulcrum developed a relationship with Flex Machine Tools after purchasing a FlexArm tapping arm about two years ago. In addition, Fulcrum’s machining center is a FlexCNC G-Series.
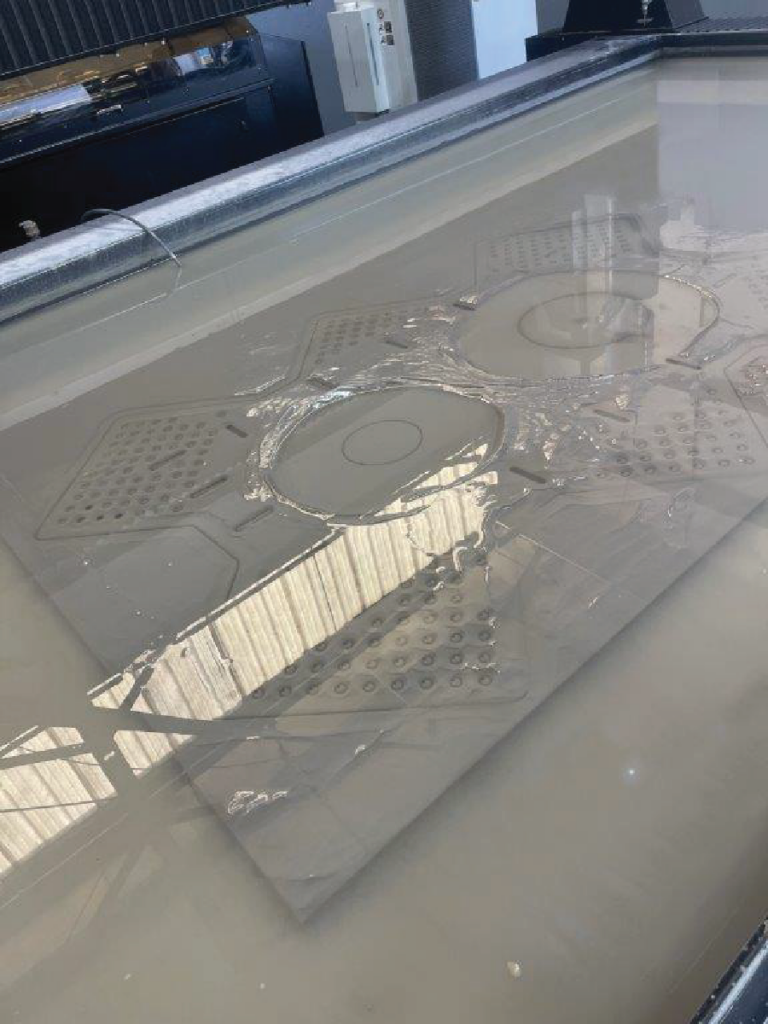
Above: Fulcrum purchased a FlexJet FLX-1365 abrasive waterjet machine with a 5-axis cutting head from Flex Machine Tools.
Flex reports that the FLX-1365 waterjet has a maximum traverse speed of 1,800 ipm, an acceleration of 0.3G and a repeatability of 0.001 in.
“It’s kind of nice to have two machines from the same supplier,” he says. “They have the same service agreement, same contract and one touch point to make sure the machines work together.”
Flex offers several waterjet series, and Fulcrum worked with the machine builder to select the appropriate one for its applications based on conversations and a site visit, Johnson says. “We were able to walk around and look at the parts and figure out what makes sense to bring in house and what doesn’t make sense. Then based on that, we were able to determine what machine was going to be the best for us.”
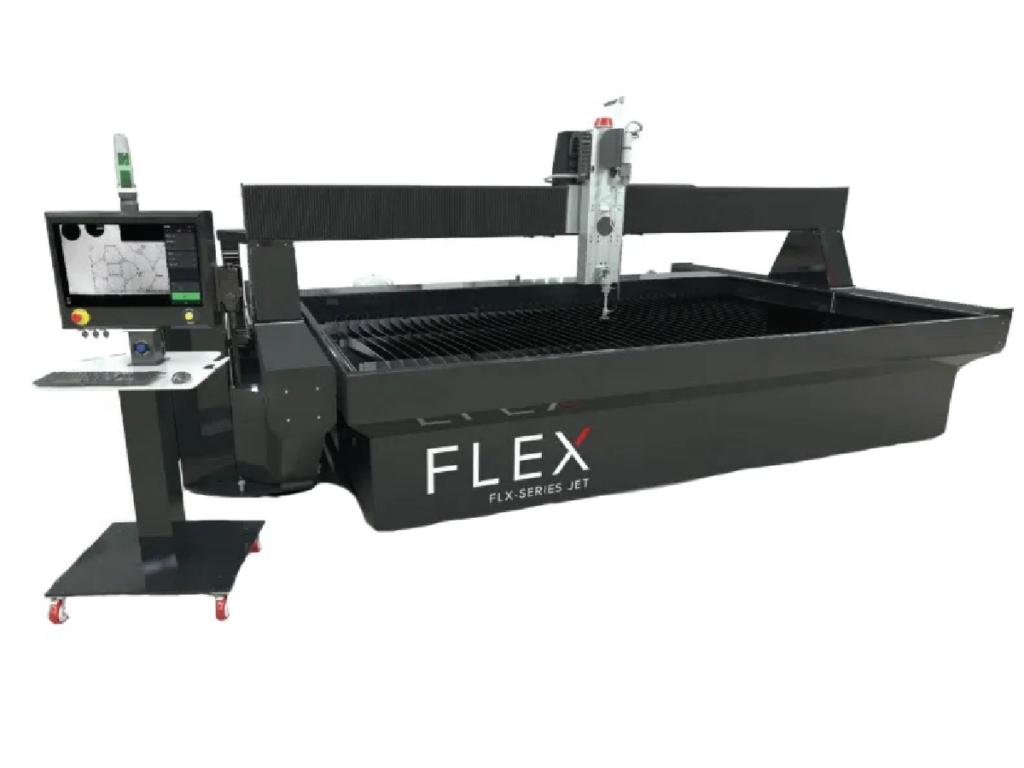
FROM THIN TO THICK
A lot of the parts cut on the waterjet are fairly large and fairly thick, with plates generally from 1- to 2-in. thick; some parts have dimensions up to 136 in., says Nick Radtke, machine shop supervisor at Fulcrum. The company also uses the waterjet to cut workpieces as thin as 20-gauge stainless steel, some carbon steel and some aluminum.
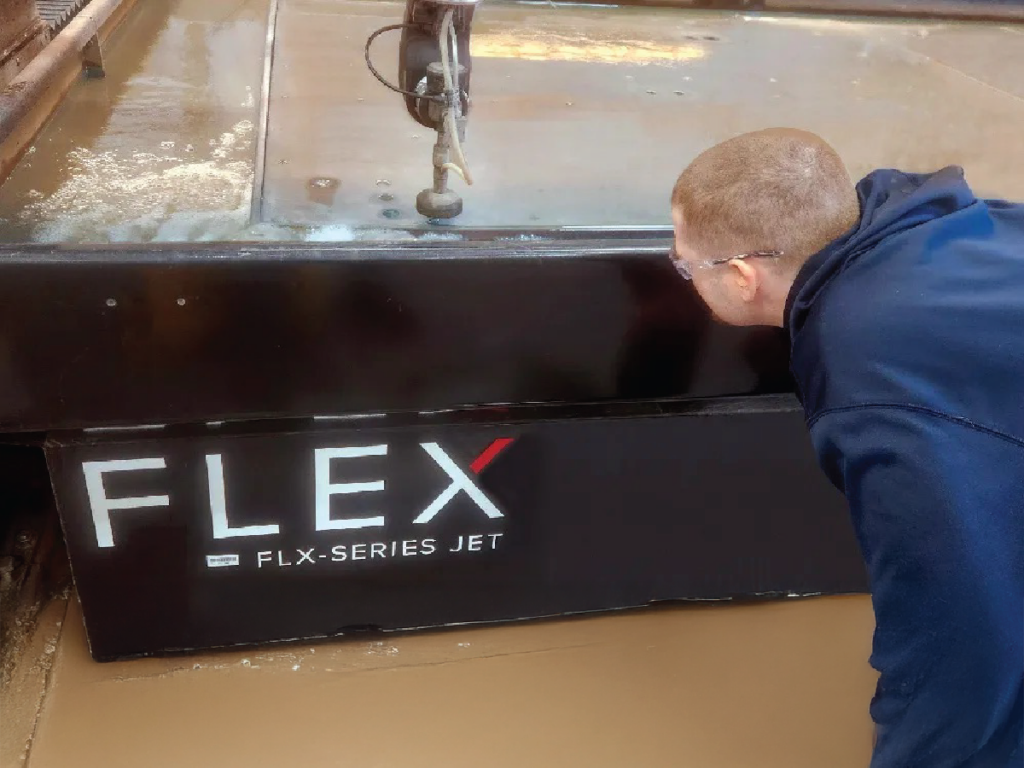
Waterjet cutting of a large workpiece is monitored at Fulcrum Technologies
The FLX-1365 with its 5-axis cutting head has X-, Y- and Z-axis movements of 156 in., 78 in. and 12 in., respectively.
Radtke notes that the 60,000-psi intensifier pump has a 50-hp motor, which is standard. Flex also offers that pump with 30-, 60- or 100-hp motor and offers 90,000- psi pumps with a 60-hp motor. However, he adds that the waterjet usually operates at a pressure of 52,000 psi. “We try not to run flat out to preserve the lifetime of the machine.”
In addition, Fulcrum cuts 1/8-in. thick acrylic vinyl tiles for cleanroom applications on the waterjet, and those are done with a water pressure of about 30,000 psi and without using garnet abrasive because it’s not needed, Radtke says.
“That was something we used to do manually,” Johnson says. “That’s taken about four or five hours out of a process by bringing it onto the machine.”
Johnson adds that Fulcrum spent time determining which manual operations can be eliminated with a waterjet, not to reduce headcount but to reduce lead times while consistently achieving tolerances as tight as ±0.002 in. and satisfying other customer part specifications. “We were able to go from a two-hour manual operation to a 13-minute operation using the machine.”
Fulcrum’s waterjet has a 5-axis head, which saves time, for example, when creating weld preps, Radtke says. “We don’t do a ton of it, but it’s a nice tool to have and relieves a lot of extra work a lot of manual work that would normally have to take place. Operators don’t have to go in and grind a 1/2-in. chamfer on a 2-in. plate to be able to get the weld that they need.”
GARNET BE GONE
When purchasing the waterjet, Radtke notes that Fulcrum selected the optional garnet removal system to extract the abrasive material and other debris. “It’s a lot better than having to drain the tank completely and having a couple of people in there, scooping out a foot and half of what’s on the bottom of the tank.”
He explains that the waterjet’s two-piece steel construction includes a helical rack-and-pinion system for improved acceleration, deceleration, accuracy and durability. That is particularly beneficial when cutting thin gauge material to maximize the pressure and cutting speed but also enables rapid toolpath-to-toolpath movements when cutting larger parts. “It’s an incredibly fast waterjet. The accuracy is phenomenal with the machine to hold pretty tight tolerances.”
Flex reports that the waterjet has a maximum traverse speed of 1,800 ipm, an acceleration of 0.3G and a repeatability of 0.001 in.
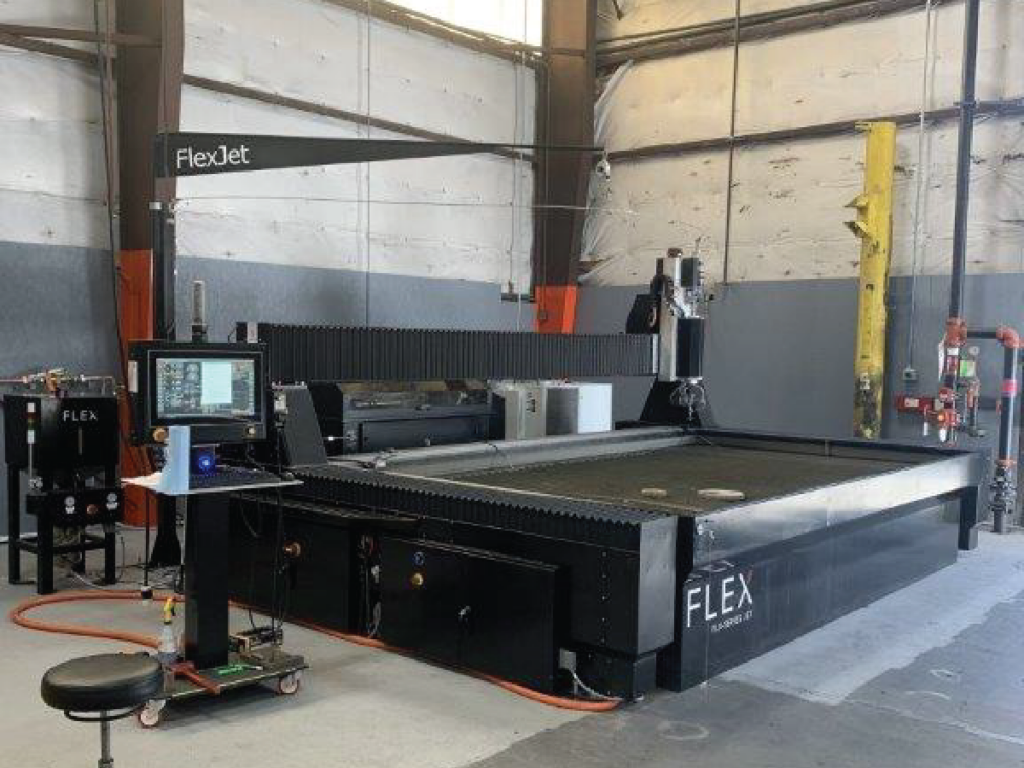
Fulcrum’s FLX-1365 waterjet machine has X-, Y- and Z-axis movements of 156 in., 78 in. and 12 in., respectively.
Another benefit of this model is the user-friendly gantry loading and unloading, Radtke notes. Instead of moving in the X-axis direction like many machines, it moves in the Y-axis direction, which enhances flexibility while clearing the gantry out of the way.
Fulcrum opted for the standard one-year service package, Radtke says, which includes a 100 percent inventory of spare and replacement parts, 24/7 remote technician support, next-business-day parts shipment and dispatch of a service technician within 48 hours.
The waterjet has run problem-free since installation last August, Radtke says.
In addition to reducing lead times, Johnson says the FLX-1365 waterjet enables Fulcrum to better control part quality.
“We’re glad we made this purchase. It has paid for itself as far as what we’re outputting and what we expect to get out of the machine.”
Fulcrum Technologies Inc., 503/691-6160, http://fulcrum-tech.net/
Written by Alan Richter, Contributing Editor
Published: March 14, 2025
Originally published in FFJournal
Visit FFJournal at www.ffjournal.net