Maintaining tight tolerances is critical for delivering quality parts, reducing scrap, and avoiding costly rework. Even the best machining centers can struggle to hold tolerances if specific variables aren’t managed consistently. Whether you’re troubleshooting a recent quality issue or just aiming to tighten your process, understanding the root causes is the first step.
Here are five of the most common reasons machining centers experience tolerance problems, and what to watch out for:
1. Thermal Expansion and Contraction
As machining operations generate heat, the machine structure and the workpiece can expand. Even small amounts of thermal growth can cause dimensions to drift outside tolerance, especially on long runs or when cutting large parts. Likewise, rapid cooling can cause contraction, leading to size variations that are difficult to predict without active temperature control or compensation strategies.
2. Worn or Loose Machine Components
Precision relies heavily on the integrity of your machine’s moving parts. Worn spindle bearings, sloppy ball screws, loose gibs, and worn ways can all introduce unintended movement or vibration. Over time, these issues compound and make it nearly impossible to produce parts consistently within spec, even if your programs and setups are perfect.
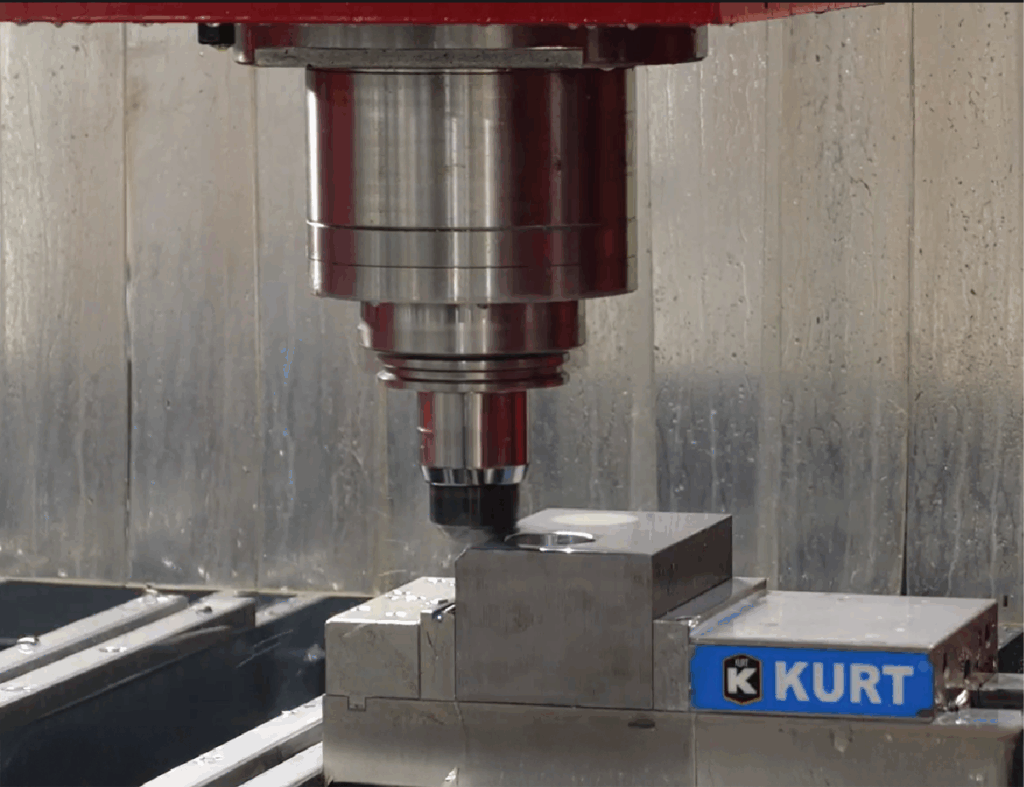
3. Improper Workholding or Fixturing
Even with a rock-solid machine, poor workholding can sabotage accuracy. If the workpiece shifts under cutting forces, dimensional errors will result. Reliable fixturing should clamp securely and minimize deflection and distortion, especially for delicate or thin-walled parts.
4. Tool Wear or Deflection
Cutting tools degrade over time; even a slightly dull tool can deflect more under load. Deflection can cause tools to cut undersize or oversize, depending on the direction of forces. In high-precision machining, even brand-new tools must be monitored closely, improper feeds and speeds can cause micro-deflection that adds up across critical dimensions.
5. Poor Machine Calibration or Setup
Accurate probing, machine leveling, and compensation for tool offsets are non-negotiable when chasing tight tolerances. Machines that haven’t been calibrated recently or set up correctly to begin with, often drift out of spec. Regular preventive maintenance and setup checks are essential to maintaining reliable performance.
How FlexCNC Helps You Hold Tighter Tolerances
While every machining operation faces these challenges, choosing the right equipment can make a significant difference. At Flex, our FlexCNC machining centers are engineered with structural rigidity, thermal stability, and precision in mind. FlexCNC machines are built to help you maintain accuracy, even on your most demanding parts, from heavy-duty construction to innovative design features that minimize heat buildup and vibration.
Curious how FlexCNC could help improve your results?
Learn more about FlexCNC machining centers here.