As published in The Fabricator on March 25, 2025. View article here.
Perhaps you are investigating a significant machine tool investment and weighing the options of different profile cutting technologies, or perhaps you have found that your current cutting capabilities are lacking, motivating you to investigate ways to broaden your services. Either way, you should realize that waterjet cutting might be a good fit. That’s why it’s helpful to review how waterjet technology has evolved, as well as dispel a few myths along the way.
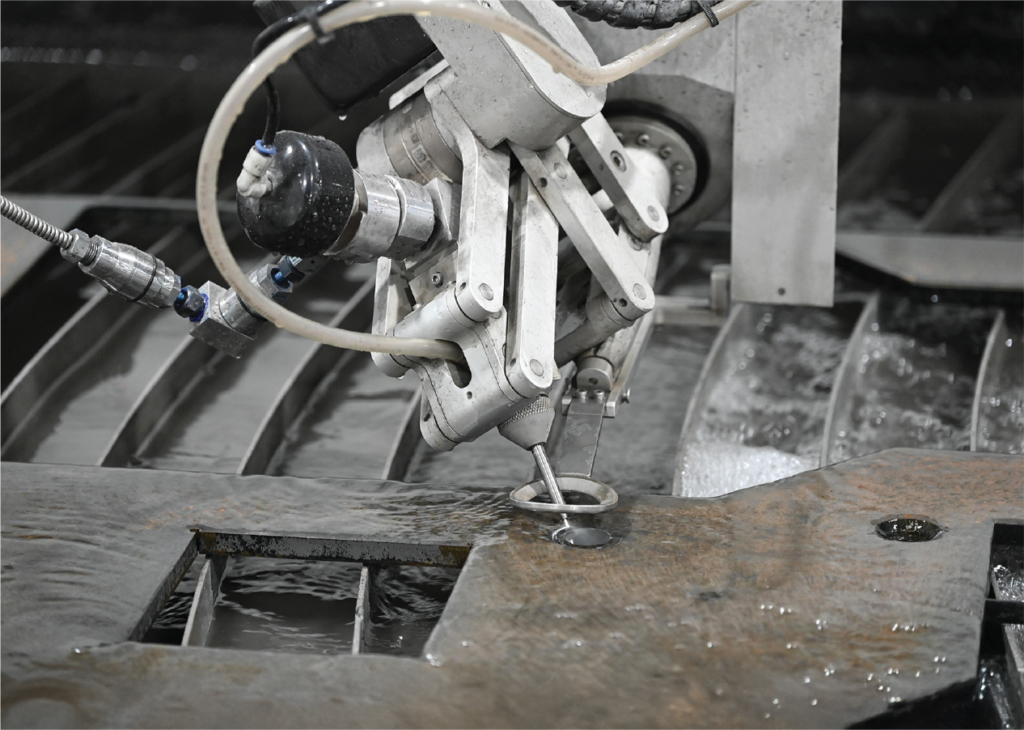
A waterjet is a versatile cutting technology that can be used to cut all kinds of metals without a heat-affected zone. The addition of the right cutting head also allows for clean-cut edges and bevels.
Waterjet cutting emerged as early as the 1930s, with low-pressure systems being used to trim paper. Technology advancements during the 20th century moved waterjet cutting capabilities forward.
During the 1940s and 1950s, the burgeoning aerospace industry saw the advancement of material science and high-pressure sealing technology, capable of operating hydraulic systems up to 100,000 PSI. The high-pressure linear intensifier pump was developed in the late ’70s, and the ’80s kicked off what can be recognized as the predecessor of the modern CNC waterjet systems that are used today. Through widespread adoption across several industries, the continued advancements in CNC systems, and refinements in cutting head and pump performance in the 1990s, 2000s, and 2010s, it is safe to say that waterjet cutting is here to stay as a fully mature manufacturing option.
That said, waterjet myths remain prevalent in manufacturing circles. That’s why it’s important for metal fabricators to understand what waterjet cutting is and isn’t. A discussion about the cutting process and the technology is a good start.
Profile Cutting Processes
When considering a waterjet purchase, you might compare several profile cutting technologies. Laser, plasma, and wire EDM are common alternatives.
A laser cutting machine typically requires the highest capital investment. With that, however, a metal fabricator gets a very fast cutting process, especially for thin materials. Because of their cutting speeds, these machines often are integrated with automated material loading systems. They also can hold a cutting tolerance of at least +/- 0.005 in.
The cost of operation is highly dependent on the type of shield gas required for each specific material being cut. Laser cutting machines are ideal when the focus is on high-volume production.
An investment in a plasma cutting system can range from quite low (air plasma) to very high (high-definition plasma). Suitable applications involve cutting mild steel up to about 2 in. thick, although advancements are continuing to be made to allow more effective cutting of stainless steel and aluminum.
Cost of operation is generally very low, but metal fabricators have to deal with heat-affected zones caused by the plasma flame, which sometimes make secondary processing difficult or require grinding of the cut edges. Part tolerance is wide, traditionally +/- 0.010 to +/- 0.060 in.
Plasma is a good choice when a wider tolerance range is acceptable or small feature sizes are not required.
The investment in wire EDM probably falls somewhere in between a laser cutting machine and a basic plasma cutting table. EDM excels in all conductive metals from very thin to very thick. Exceptionally high tolerances are possible, +/- 0.0001 in. in some cases, but the process is very slow. Additionally, start holes must be predrilled for interior contours.
The low hourly cost of operation often is offset by long run-times. Wire EDM is the de facto cutting choice when the tightest possible part tolerances are required, especially in thicker materials.
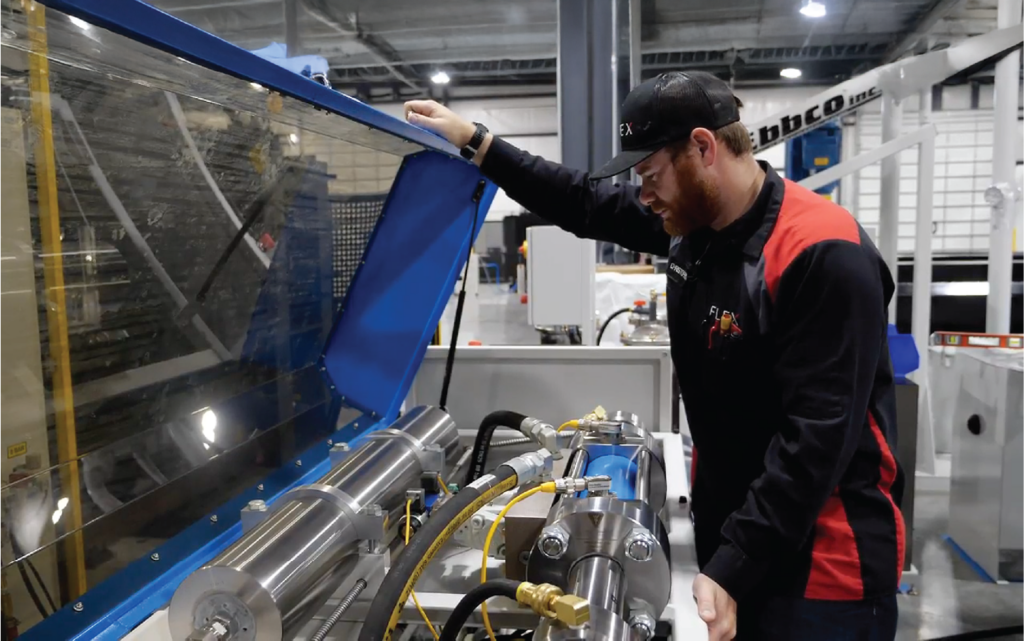
Despite waterjet pump technology improving since the 1990s and 2000s, regular maintenance is still required, particularly on high-pressure pumps.
What Is Waterjet Cutting?
Having defined a few complementary cutting technologies, what is waterjet cutting? In short, abrasive waterjet cutting is a highly controlled, accelerated erosion process. Water pressurized from 60,000 to 90,000 PSI passes through a small jewel orifice to create a supersonic jet stream. Abrasive media, most often crushed garnet, is introduced into this jet and focused through a nozzle. The resultant waterjet stream is typically 0.030 to 0.040 in. dia.
Waterjet cutting has a few distinct advantages when compared to other cutting processes:
- For an investment of $100,000 to $500,000, a metal fabricator can purchase equipment that can cut material of any thickness.
- A waterjet can cut any material: ferrous or nonferrous, brittle or ductile, and uniform or composite.
- While tighter tolerances are possible, +/- 0.005 in. is easily achievable in nearly all materials less than 2 in. thick, with no tooling changeovers required and no physical, thermal, or chemical alterations made to the workpiece.
Waterjet Technology: Fact or Fiction?
Many stereotypes surrounding the waterjet cutting process linger in manufacturing. Most stem from the early days of the technology. While some of these myths emanated from kernels of truth back in the day, waterjet technology has progressed, and best practices have evolved. Let’s talk about some of these myths.
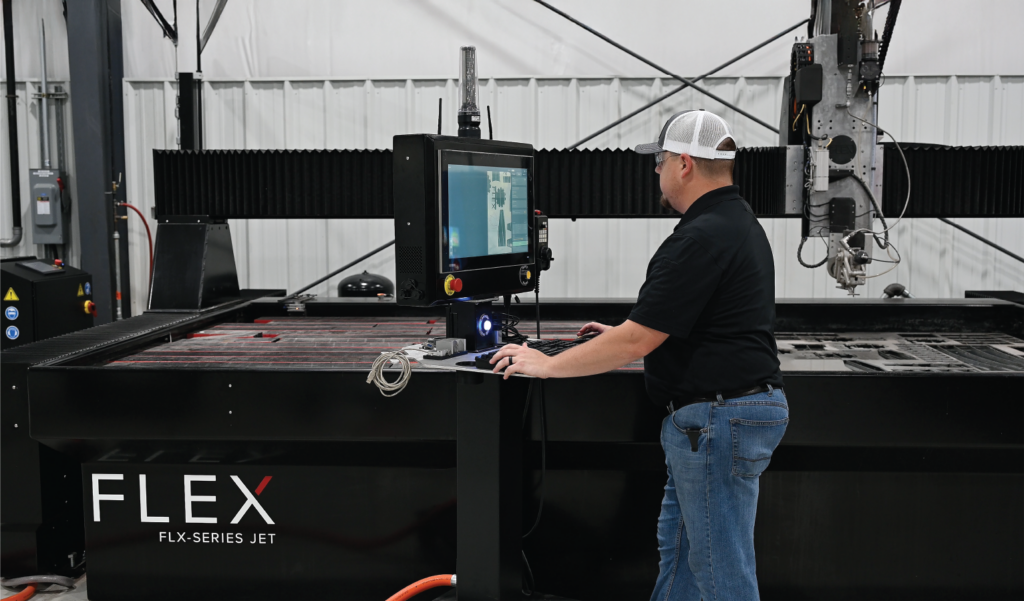
A modern controller and CAM system specifically designed for waterjet will deliver better results than software designed for another cutting process that was adapted for waterjet cutting.
Waterjet Cutting Is Loud. Anyone who has been around a waterjet may have been subjected to the roar of the cutting stream or whine of the high-pressure pump. The sound of the cutting stream is easily mitigated by a little understanding of the physics of the process.
As stated earlier, when a pressurized waterjet (potential energy) is forced through an orifice and exits the cutting head, a high-velocity stream is generated (kinetic energy). Depending on the system operating pressure, this stream is moving at Mach 2, Mach 3, or even Mach 4! This supersonic stream of water pulls the surrounding air into itself, which creates a loud shearing noise. If a typical waterjet stream is fired into free air, as opposed to a waterjet catch tank, sound meter readings can reach upwards of 120 dB. That jet engine sound is loud!
The solution is simple: Minimize or eliminate the amount of air around the jet to drastically reduce the sound. To do this, keep the catch tank water high and in contact with the bottom of the material to control sound. An air gap under the material is the single largest contributor to operational noise.
A metal fabricator also could flood the material during the waterjet cutting process. Cutting underwater is a great tactic for reducing noise even further.
Regarding pump noise, most of the sound is generated from the shifting of the hydraulic system. Hydraulic pump design, shift valve design, and oil cooling systems all have improved since the early days. Do not make the mistake of assuming all pumps are equal, or an industry design from 20 years ago operates the same as today’s designs.
Employing a modern intensifier along with good management of the catch tank’s water level results in a cutting system operating below 90 dB. Sounds can be reduced further with proper cutting head nozzle and machine guarding.
Waterjet Cutting Is Messy. With a little attention to detail, a shop can keep its waterjet system operating cleanly. All it has to do is focus on the two main contributors to the mess-making: job setup and catch tank cleanliness.
A supersonic jet stream not only has the potential to create an ear-piercing noise, but it also can create a great amount of turbulence in the waterjet tank. While the waterjet stream naturally causes a turbulent upwell of fluid in the catch tank, the addition of a large volume of air greatly exacerbates this issue, resulting in splashing. Similar to reducing noise, keeping a high water level in the tank is the best way to control this.
Also, installing a piercing cone around the cutting head nozzle not only helps with sound control but also contains splash-back during the initial pierce cycle.
The second piece of this puzzle, and one that often is overlooked, is the overall cleanliness of the catch tank. Abrasive buildup from the cutting process is unavoidable. After all, it is one of the primary functions of the tank. Removing this abrasive regularly and keeping it to a reasonable level go a long way in keeping a shop clean. Regular tank dig-outs or investing in an automatic abrasive removal system can help with maintaining a clean shop while running a waterjet.
Waterjets Are Expensive to Operate. An easy trap for a metal fabricator to fall into while investigating cutting technologies is to compare processes without analyzing the total cost to manufacture a part.
While waterjet cutting might be slower than laser or plasma when processing certain materials, the lack of a HAZ might completely remove secondary operations needed to finish a part. Eliminating a grinding and cleanup step or having the ability to tap a small hole directly off the waterjet are two examples of secondary processes that have been eliminated because waterjets are able to address them on the cutting table.
A waterjet can finish a profile cut 10 times faster than wire EDM. Also, incorporating a second operation to clean up a critical surface often can be more economical than producing a finished part with EDM alone.
While it will vary with specific equipment and applications, a good starting point when determining a waterjet’s cost of operation is approximately $30 to $35 per hour. For more concrete information, reach out to a waterjet sales representative or an industry expert to conduct a time study to help determine accurate part costs for your specific application.
Waterjets Offer Poor Cut Quality. Waterjets are what the industry refers to as soft tools. In other words, the stream is not rigid like an EDM wire or conventional end mill. As it moves through a material, the exit of the jet from the bottom of the workpiece lags behind the direction of motion. This is known as trailback angle. The stream also does not maintain its round or columnar shape; it is squished down and ovalized.
The math models for understanding the physics of both phenomena are complex but are now well defined and understood by those in the industry. Purchasing a machine with a modern controller and CAM system that is specifically designed for waterjet incorporates these models and yields the good part quality. The old nesting software running the plasma system or the add-on post from your software value-added reseller might technically generate a code to run a waterjet, but the results are almost always disappointing.
Because it is erosive, waterjet has an extreme range of possible cut qualities for any given material. Surface finishes of 100 to 125 RMS with square, draft-free edges are achievable with proper software and multiaxis cutting heads that offer automatic taper angle control. (RMS stands for root mean square, a method of measuring the roughness of a surface. More specifically, it’s used to calculate the average roughness of a surface by measuring the height of its peaks and valleys.)
Waterjet Pumps Require Significant Maintenance. Pump maintenance often is a loaded subject, and you can easily find people who are happy to share their horror stories. Short seal life and failed check valves are at the center of many of these stories. With some digging, the root cause of these failures often boils down to shortcomings in early pump designs and proper training.
Waterjet adoption exploded in the 1990s and 2000s. Pump designs from this era are now off-patent, leading some companies to still manufacture these designs today. As a result, there are tens of thousands of these pumps in North America alone.
But just because something is most common does not mean it is the best. Engineering advancements have improved every wear component in modern pumps, and life expectancy has increased across the board. Pump seals are the weakest link in any high-pressure system and will be the first item to fail if something is wrong. They are your canary in the coal mine. Short seal life will often point to bad water quality, worn components elsewhere in the system, or poor maintenance practices.
Focus on the Facts
Understanding the facts of waterjet cutting is helpful when considering its implementation. Its versatility and improved technology make it a wise choice for many metal fabricators with the right mix of work.
A waterjet OEM or supplier not only can provide more in-depth details about the mechanics of the equipment, but it also can discuss how the waterjet can help with your specific application. Putting in some effort to understand the process and then scheduling a test cut or time study are well worth the time.
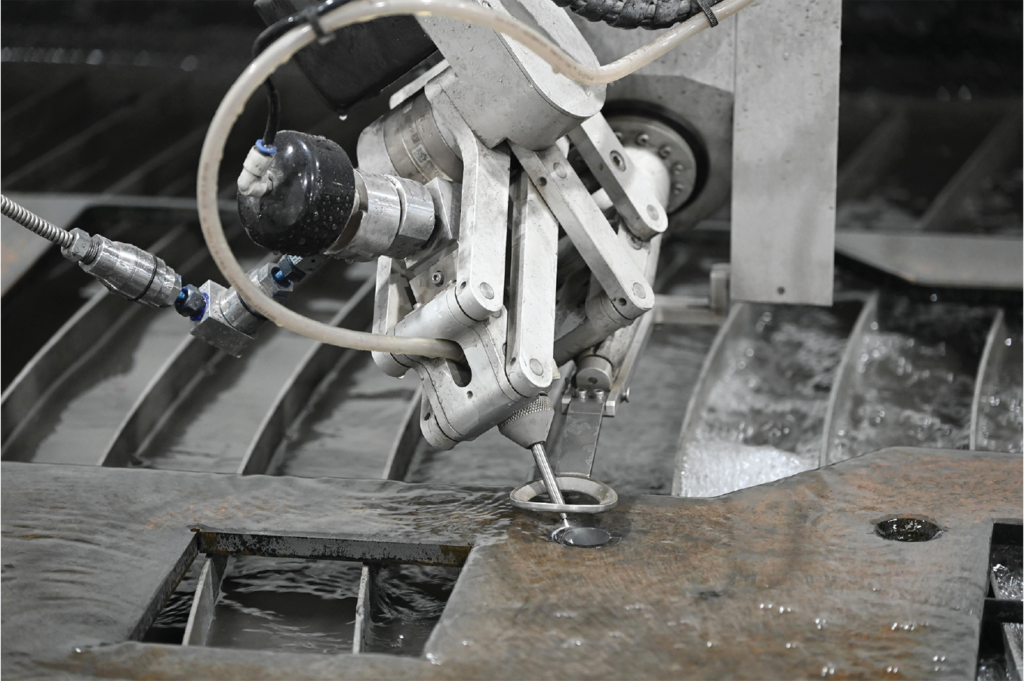
Written by Jason Stuffel
Regional Sales Manager
Flex Machine Tools